Plant Engineering Why Should You Choose a Modular Plant?
Related Vendors
Cost plays a vital role while developing industrial plants but by opting for a modular plant, capex costs, material costs and even labor costs can be slashed. Also, modular, skid-mounted units are developed in-doors under controlled environments and at speed which helps to save valuable time for industry players.
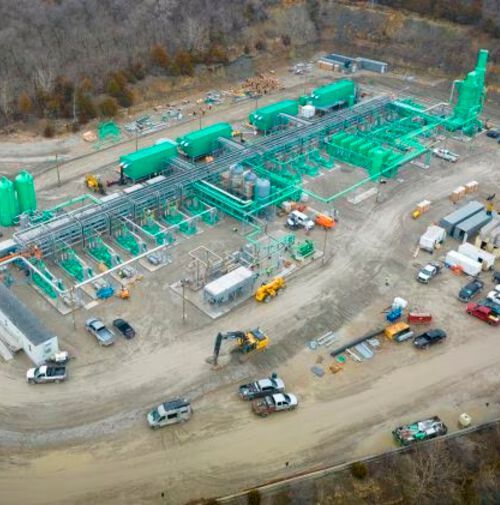
The world’s largest direct air capture plant has recently begun operations in Iceland. Named ‘Mammoth’, the mega facility by Climeworks is designed for a nameplate capture capacity of up to 36,000 tons of CO₂ annually and is modular in design. Next, the world’s largest ‘ammonia to hydrogen’ modular cracker demo is in operation. Expected to deliver 140 tonnes of fuel cell grade hydrogen per annum, the demo unit has been designed, built and commissioned by AFC Energy. These two landmark projects have one thing in common i.e. both of them are modular in design.
Modular units are developed off-site and pre-fabricated with numerous or single technologies and equipment such as process equipment, instrumentation, valves, piping components, and electrical wiring (as per the project requirement) which are installed on skids (steel framework). The skid-mounted units are transported to the on-site location and then connected.
Sign in or register and read on
Please log in or register and read this article. To be able to read this article in full, you must be registered. Free registration gives you access to exclusive specialist information.
Already registered? Log in here