Plant Watch Top 10 Engineering Projects of April 2024
Related Vendors
PROCESS Worldwide brings to you the ‘Top 10 plant engineering projects of April 2024’ from all over the world. Right from the MOL Group inaugurating one of the largest green hydrogen plants in Europe to BASF, Sabic and Linde starting up the world’s first large-scale electrically heated steam cracking furnace, find out all the projects making headlines here.
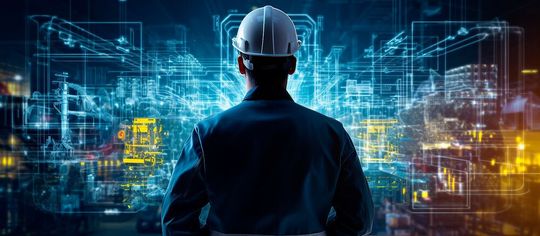
Ecolab Inaugurates New Wastewater Treatment Plant in Singapore
April 01 – Nalco Water, Ecolab's water brand, has recently announced the opening of a wastewater treatment plant in Shell Jurong Island, Singapore. Commencing operations earlier this year, this facility is designed to handle variable bio-treater wastewater. The plant utilizes Ecolab's ultrafiltration and reverse osmosis (RO) membrane system and is almost 100 % automated.
With the capacity to treat and reuse up to 24,000 cubic metres of wastewater every month, the facility stands as a testament to Ecolab's commitment to helping customers move toward responsible water consumption.
Gregory Lukasik, senior vice president and Market Head of Southeast Asia, Ecolab said: "We're thrilled to have achieved this key milestone, demonstrating once again that sustainability and business performance can be pursued in tandem. By focusing on water at an enterprise level, companies can identify opportunities that meet both their sustainability and business goals. Aligned with Ecolab's focus on impactful goals, including saving 300 billion gallons of water by 2030, we're proud to support our valued customers in promoting responsible water consumption and contributing to Singapore's sustainable future."
Neste to Begin Major Turnaround of Porvoo Refinery in Finland
April 03 – At Neste’s refinery in Porvoo, Finland, the preparations for the major turnaround taking place in April-June began on 1 April with shutdowns of process units. After the refinery shutdown is completed, the actual turnaround works will begin in mid-April and are expected to continue until mid-May. The estimated duration of the turnaround is approximately nine weeks.
During the major turnaround, the entire Porvoo refinery will be shut down for statutory inspections, maintenance works and asset improvement initiatives. In addition, the turnaround will contribute to Neste's ambition to make the Porvoo refinery the most sustainable refinery in Europe by 2030 and to reach carbon-neutral production by 2035. The major turnaround does not affect Neste’s harbor and distribution terminal operations.
Careful planning has enabled Neste to shorten the duration of the 2024 major turnaround compared to previous major turnarounds in Porvoo. Shutdowns and startups of process units temporarily cause increased flaring, noise and odor nuisance in the nearby areas. During the major shutdown, traffic volumes in the nearby area increase considerably.
Nuberg EPC Wins EPCM Contract for India’s Largest Chlor-Alkali Project
April 15 – Nuberg EPC has announced its latest undertaking: India’s largest Chlor-Alkali project, commissioned by Mundra Petrochemical Ltd. (MPL), a subsidiary of Adani Enterprises. This pioneering project is poised to make a significant impact in the industry with a capacity of 2200 TPD, utilizing a 100 % NaOH process.
Strategically located in the vibrant Mundra zone of Gujarat, the project stands as a testament to innovation and engineering excellence. It is meticulously designed to produce a range of essential chemicals, including 50 % caustic soda, caustic flakes, anhydrous HCl, and liquid Cl2. The plant will also yield by-products such as 31 % HCl acid, 32 % NaOH, Sodium Hypochlorite, and H2SO4, which are crucial to MPL’s expanding Green PVC Project.
The project was signed off with a high-profile meeting in Mumbai, graced by the presence of Adani Enterprises’ dignitaries, including Jeet Adani, Vice President; Jayant Parimal, CEO; Jagan Kishore, Project Director; Upendra Varmora, Techno-commercial Head; and Nimai Charan, VP Project Manager; as well as Nuberg EPC’s luminaries, Amit Tyagi, Director; and Rakesh Verma, Chief Business Development Officer.
Committed to swift delivery within a 15-month period, Nuberg EPC’s engagement covers the full gamut of EPCM services, ensuring unparalleled quality and efficiency. This Chlor-Alkali plant is more than just a project; it represents India’s industrial fortitude and is a key element in the production of feedstocks for MPL’s comprehensive suite of refineries and chemical plants, symbolizing Nuberg EPC’s steadfast commitment to driving India’s industrial advancement.
MOL Group Inaugurates One of the Largest Green Hydrogen Plants in Europe
April 16 – MOL Group has handed over a 10-megawatt capacity green hydrogen plant in Százhalombatta, Hungary which is the largest in Central and Eastern Europe. The 22-million-euro investment makes fuel production more sustainable: the plant will reduce the Danube Refinery's carbon dioxide emissions by 25,000 tonnes. MOL will be able to produce 1,600 tonnes of clean, carbon-neutral green hydrogen per year which opens a new chapter in hydrogen economy. The investment is in line with the MOL Group's ‘Shape Tomorrow’ corporate strategy to make the region more sustainable, competitive and self-sufficient.
MOL Group’s goal is to provide the solutions for tomorrow: the green hydrogen plant in Százhalombatta, with a 10-megawatt electrolysis unit created by Plug Power produces around 1,600 tonnes of clean, carbon-neutral green hydrogen per year. The 22 million-euro investment will reduce the carbon footprint of the Danube Refinery by more than 25,000 tonnes of carbon dioxide per year. The new technology will gradually replace the natural gas-based production process, which currently accounts for one sixth of the MOL Group's total carbon dioxide emissions. The plant will start producing in the second half of 2024: MOL will use the green hydrogen primarily in its own network for fuel production.
Plug Power's electrolysis equipment uses electricity from renewable sources to break down water into hydrogen and oxygen. This means that no polluting by-products are generated and, in fact, the plant produces 8-9 tonnes of pure oxygen per tonne of hydrogen. The US company has offered MOL an innovative and reliable technology: the hydrogen generators, optimized for the production of pure hydrogen, have almost 50 years of operational experience.
BASF, Sabic, Linde Start-Up World’s First Large-Scale Electrically Heated Steam Cracking Furnace
April 18 – BASF, Sabic, and Linde have inaugurated the world’s first demonstration plant for large-scale electrically heated steam cracking furnaces. Following three years of development, engineering, and construction work, the regular operation of the demonstration plant is now ready to start at BASF’s Verbund site in Ludwigshafen, Germany. In March 2021, the three companies signed a joint agreement to develop and demonstrate solutions for electrically heated steam cracking furnaces.
Steam crackers play a central role in the production of basic chemicals and require a significant amount of energy to break down hydrocarbons into olefins and aromatics. Typically, the reaction is conducted in furnaces at temperatures of about 850 degrees Celsius. Up to now, these temperatures have been reached by using conventional fuels. The demonstration plant aims to show that continuous olefin production is possible using electricity as a heat source. By using electricity from renewable sources, the new technology has the potential to reduce CO2 emissions of one of the most energy-intensive production processes in the chemical industry by at least 90 % compared to technologies commonly used today.
The demonstration plant, which produces olefins, such as ethylene, propylene, and possibly also higher olefins from saturated hydrocarbon feedstock, is fully integrated into the existing steam crackers in Ludwigshafen. The upcoming operation serves the goal of gathering data and experiences about material behavior and processes under commercial operating conditions for the final development of this innovative technology to industrial market maturity. In two separate demonstration furnaces, two different heating concepts will be tested.
While in one furnace, direct heating applies an electric current directly to the cracking coils, in the second furnace, indirect heating uses radiative heat of heating elements placed around the coils. The two electrically heated furnaces together process around 4 tons of hydrocarbon feedstock per hour and consume 6 megawatts of renewable energy.
To support the development of the novel furnace technology, the project was granted 14.8 million euros by the German Federal Ministry for Economic Affairs and Climate Action under its “Decarbonization in Industry” funding program. The program is supporting energy-intensive industries in Germany in their efforts to achieve carbon neutrality.
Lyondell Basell, Genox Launch Plastics Recycling Joint Venture
April 23 – Lyondell Basell has announced the opening of the plastics recycling joint venture (JV) in Zhaoqing, Guangdong Province in Southern China with Genox Recycling (Genox). The plastic recycling plant will use mechanical recycling technology to recycle plastic waste and produce new polymers, adding to the Lyondell Basell Circulen Recover product portfolio. The JV will operate under the name Guangdong Genox Lyondell Basell New Material Co.
“Today’s announcement demonstrates our progress on recycling investments. This joint venture is linked to Lyondell Basell’s commitment to support a circular economy for plastics and is part of our strategy to expand our circular polymer offering in China,” said Yvonne van der Laan, Lyondell Basell executive vice president, Circular and Low Carbon Solutions. “This partnership with Genox enables us to create local recycling solutions for customers and brand owners in China in support of their ambitious targets.”
“Today we celebrate the opening of our pioneering joint venture facility with valued partners, customers, employees and local stakeholders,” said Allen Yu, Lyondell Basell senior vice president, Asia Pacific. “The JV opening demonstrates our determination to support the growth of our customers in the region by driving sustainable solutions together with our partners.”
“This new JV is an execution of Lyondell Basell’s strategy of building a strong and profitable Circular and Low Carbon Solutions business in Asia”, said Limin Fu, vice president of Lyondell Basell China’s Joint Venture Management and Polyolefins, chairman of Guangdong Genox Lyondell Basell New Material Co. “The JV combines the strengths of both shareholders to deliver the result we see today. This includes partnering with Genox through an off-take business, developing innovative products to meet customer’s needs, growing our capability into the entire plastics recycling value chain. This new joint venture will help develop the local plastics recycling infrastructure in China and contribute to a circular economy.”
KBR Secures Contract for Sabic's Phenol Plant in China
April 23 – sKBR has been awarded a contract by Sabic Fujian Petrochemicals to license KBR's market-leading phenol technology in China. Under the terms of the contract, KBR will provide technology licensing and proprietary engineering design for a 250 KTA phenol plant at Sabic's Fujian Petrochemical Complex. The final investment decision for this project was announced in January 2024 with expected completion in FY 2026. KBR's phenol technology offers a sustainable and differentiated solution through reduced energy consumption and improved yields.
"We are excited to offer our industry leading phenol technology to Sabic Fujian for this ambitious project in China," said Jay Ibrahim, President, KBR Sustainable Technology Solutions. "KBR's market-leading phenol technology increases our customers' competitive advantage and advances their sustainability objectives through superior efficiency, reliability, wastewater recovery and performance."
IOCL Selects Lummus Technology for New Cumene Unit in India
April 25 – Lummus Technology has announced that Indian Oil Corp. Ltd. (IOCL) has selected the Lummus/Versalis cumene technology for a 440 KTA unit in Paradip, India. The new cumene unit is part of a grassroots petrochemical and polymers expansion at Indian Oil’s complex in Paradip.
“Our cumene technology will offer Indian Oil lower energy costs, reliability, operational efficiency and exceptional product yield, which will help them optimize their plant economics and support their growth initiatives,” said Romain Lemoine, Chief Business Officer for Polymers and Petrochemicals, Lummus Technology. “We look forward to continue working with Indian Oil on another successful project and building on our long-time relationship.”
Lummus’ scope includes the technology license for the cumene technology, basic design engineering, proprietary catalyst, site services, advisory services, and training.
Indian Oil has licensed multiple Lummus technologies, including naphtha cracker, Indmax FCC and polypropylene technologies at its complexes across India.
Lummus and Versalis have partnered to license cumene technologies since 2007. The cumene process is a liquid-phase alkylation technology using a proprietary zeolite catalyst and is characterized by a very high cumene yield, ultra-high purity cumene product and a long catalyst run length.
Syensqo Breaks Ground on Largest PVDF Production Unit in North America
April 29 – Syensqo recently broke ground on its future battery-grade polyvinylidene fluoride (PVDF) facility in Augusta, Georgia, USA. They were joined by Tom Perez, Senior Advisor and Assistant to the President and Director of the White House Office of Intergovernmental Affairs, and by Giulia Siccardo, Director of the Department of Energy’s Office of Manufacturing and Energy Supply Chains, as well as other representatives. The critical support of the Biden-Harris Administration underscores the project's significance for the U.S. EV market.
When complete, the site will be the largest PVDF production facility in North America, supplying the growing needs of domestic energy storage markets. A significant milestone in Syensqo’s global electrification strategy, this facility will help create battery materials needed to unlock economy-wide electrification and electric vehicle (EV) adoption. PVDF is a thermoplastic fluoropolymer that is used as a lithium-ion binder and separator coating in batteries. Specifically, the new site will produce Solef,
Syensqo’s signature PVDF product, which enables EVs to go farther on each charge, extends battery life and improves battery safety.
The site is estimated to produce enough PVDF for more than 5 million EV batteries per year at full capacity, or 45 percent of expected PVDF demand required by 2030, creating a new and reliable supply for the rapidly growing U.S. EV battery market, as well as hundreds of jobs throughout the value chain.
Topsoe Technology Selected for SAF Production in China
April 30 – Topsoe has signed an agreement with Guangxi Hongkun Biomass to provide its Hydroflex technology to produce SAF at the company’s plant in the Qinzhou Port Area Free Trade Pilot Zone of Guangxi, China. This agreement is Topsoe’s first SAF project in China.
Topsoe will deliver its Hydroflex technology for the project, which expects to process 300,000 tons of feedstock per year. Guangxi Hongkun Biomass’ SAF production plant is expected to begin construction in May 2024, with SAF production to begin within the first few months of 2026.
Elena Scaltritti, Chief Commercial Officer at Topsoe, said: “We continue to expand our SAF technology offering across the world, and we are thrilled to secure our first agreement to supply SAF production technology to a partner in China. This agreement represents a key step in introducing an alternative to conventional jet fuel in this geography and contributes to our sustained efforts of supporting decarbonization globally. We look forward to further expand our relationship with Guangxi Hongkun Biomass to achieve their decarbonization goals.”
(ID:50020796)