Plant Watch Top 10 Projects of February 2024
Related Vendors
PROCESS Worldwide brings to you the ‘Top 10 plant engineering projects of February 2024’ from all over the world. Right from Chevron Lummus Global commissioning the world’s largest all-hydroprocessing white oil unit to Lanzajet inaugurating the world’s first ethanol to SAF production facility, find out all the projects making headlines here.
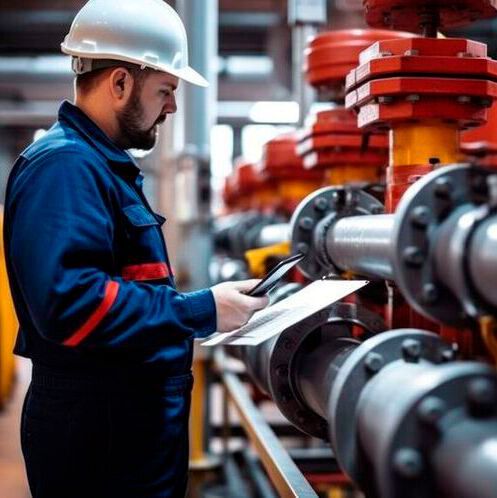
CLG Commissions World's Largest All-Hydroprocessing White Oil Unit
Feb 01 – Chevron Lummus Global (CLG) has recently announced the successful commissioning of the world's largest white oil hydroprocessing unit for Hongrun Petrochemical (Weifang) Co. in Weifang, Shandong Province, China. The new plant, which utilizes CLG's Isodewaxing and Isofinishing technologies, consists of two units: a 500,000-metric-tons per annum (MTPA) nameplate capacity API Group III lubricating base oil unit with the capability to produce industrial-grade white oil, and a 200,000 metric tons per annum nameplate capacity food grade white oil unit.
White oil is a highly refined mineral oil that is used in a wide variety of applications, including pharmaceuticals, cosmetics, food processing and industrial lubricants. Food-grade white oil is a special type of white oil that is manufactured to meet the strict purity requirements of the food and beverage industry.
Air Liquide to Invest 40 Million Euros for Modernization of Assets
Feb 09 – Air Liquide and Dow have renewed their industrial gas supply agreement in Stade, one of the largest chemical production sites in Lower Saxony, Germany. In this context, Air Liquide will supply industrial gases under a long-term agreement and invest close to 40 million euros in the modernization of its assets, enabling operational efficiency and reducing CO₂ emissions.
As part of the agreement, Air Liquide will modernize its existing production assets - two Air Separation Units (ASU) as well as one Partial Oxidation plant (POX), to which it will add a new CO₂ recycling solution. This will enable a circular use of the CO₂ produced, leading to around 15 % increase in energy efficiency and reducing the emissions by around 15,000 tonnes/year, which represents 80 % of direct CO₂ emissions of the Air Liquide site. The modernization of these assets will be completed in 2024. Air Liquide has been supplying industrial gases to Dow in Stade, Germany, for more than 20 years.
MHI, Worley Win Contract for UK’s First CO2 Capture Plant at Cement Production Unit
Feb 09 – Mitsubishi Heavy Industries (MHI)'s technology is being deployed by leading global cement manufacturer Heidelberg Materials UK, for Front End Engineering Design (Feed), to further study the specifications of a CO2 capture plant at Padeswood Cement Works in Flintshire, UK. This contract has been awarded in accordance with the progress made by the Padeswood CCS (carbon capture and storage) project planned for the site. MHI was selected after working on the initial competitive Pre-Feed (Note) project study awarded in 2022.
The project is part of the Hynet CCUS (carbon capture, utilization and storage) cluster in the North West of the UK, which plans to capture up to 800,000 tons of CO2 annually from flue gas produced during the cement manufacturing process and store it in a depleted gas field off Liverpool Bay. The CO2 capture plant could start operation in 2028. As well as the direct benefit of decarbonizing the industrial process, enabling the production of carbon neutral cement is key to supporting a low carbon supply chain to the construction industry.
This project is a partnership between MHI and Worley, a global professional services company of energy, chemicals and resources experts, and will implement the basic design of the CO2 capture plant using the "Advanced KM CDR Process" proprietary CO2 capture technology developed jointly with The Kansai Electric Power Co.
Introducing World’s First Pilot Plant for Bio-Based Aniline
Feb 14 – Covestro is moving forward with the implementation of a unique process for producing the important chemical aniline entirely based on plant biomass instead of petroleum for the first time. At its Leverkusen site, the plastics manufacturer has now put a special pilot plant into operation for this purpose.
Initially, large quantities of bio-based aniline will be produced there, so that the new technology can be further developed for production and transferred to an industrial scale. In the plastics industry, aniline is used to produce MDI, among other things. This in turn is used for insulating foam, for example, which saves energy in buildings and reduces the CO2 footprint. Covestro believes it will contribute to the promotion of the circular economy, which the company is aiming to become fully aligned with.
“Among other things, aniline is a key raw material for foams used to insulate buildings and refrigerators,” explained Dreier, on the significance of the base chemical. “Until now, aniline has been produced from fossil raw materials such as petroleum, which releases CO2 and fuels climate change. With our new process, we are contributing to building up a circular, bio-based economy, and I am very proud that we have now succeeded in making the jump to the next technological level.”
Covestro developed the process, which has already won several awards, together with partners in the scientific community. Compared to conventional technology, the process leads to a greatly improved CO2 footprint of aniline. Covestro has made a seven-digit investment in the pilot plant at the Chempark Leverkusen.
The project also clearly showcases the potential contribution of the industrial (“white”) biotechnology to plastics production: in the new process, a customized microorganism helps convert an industrial sugar extracted from plants into an intermediate product through fermentation. This takes place under milder and thus more environmentally compatible conditions than in conventional processes. In a second step, chemical catalysis of the intermediate product then creates the aniline with one hundred percent plant-based carbon.
Lanzajet Inaugurates World’s First Ethanol to SAF Production Facility
Feb 15 – Lanzajet recently joined government officials, industry leaders, partners, and supporters to open Lanzajet Freedom Pines Fuels, the world’s first ethanol to sustainable aviation fuel (SAF) production facility. Lanzajet’s technology is recognized as the pioneering ethanol to SAF production process and pathway. This ethanol-based technology is the world’s first viable next-generation SAF technology capable of scaling production to the levels needed to decarbonize aviation through widely available and sustainable feedstock, emerging commercial waste-based feedstock solutions, and promising economic conditions.
Located in Soperton, Georgia, Lanzajet Freedom Pines Fuels represents one of the most promising SAF technologies in nearly a decade to reach commercial readiness, and will produce 10 million gallons of SAF and renewable diesel per year from low carbon, sustainable, and certified ethanol which meets U.S. and global standards. Lanzajet’s technology enables current and future supply volume to support a scaled SAF industry as well as the White House’s SAF Grand Challenge, which calls for a supply of at least 3 billion gallons of SAF annually by 2030 to tangibly reduce aviation emissions. With its proprietary ethanol to SAF technology, Lanzajet Freedom Pines Fuels serves as a blueprint for utilizing first-of-its-kind innovation to scale SAF production and combat the worsening climate crisis.
The SAF produced by Lanzajet in Soperton, Georgia will be used immediately as drop-in fuel for existing aircraft in an aviation industry, which contributes two to three percent of all global greenhouse gas emissions from humans. The technology used at Lanzajet Freedom Pines Fuels will reduce greenhouse gas emissions by more than 70 percent and produced from a variety of sustainable feedstocks, such as agricultural waste, municipal solid waste, energy crops, carbon captured from industrial processes, and more.
Fluor Secures Contract for World’s First Renewable Hydrogen-based Integrated Steel Mill
Feb 16 – Fluor Corporation has recently announced that H2 Green Steel has selected Fluor to provide engineering, procurement and construction management services at the world's first renewable hydrogen-based integrated ‘green steel’ mill in Boden, Sweden. Fluor’s scope includes a melt shop, casting, rolling and finishing facilities for the project’s steelmaking plant. The H2 Green Steel site will produce five million tonnes of steel annually by 2030, with up to 95 % less CO2 emissions compared to steel produced using traditional blast furnace technology.
“The execution of the H2 Green Steel project will build on Fluor’s long-term presence in the steel industry, our expertise in novel, low-emissions steelmaking technologies and our strong presence in Europe,” said Harish Jammula, President of Fluor’s Mining & Metals business line. “We are excited to be part of this important project and to support H2 Green Steel on their journey to sustainable steelmaking.”
Construction of the mill has already begun.
Qatar Energy, Chevron Phillips Chemical to Develop Mega Polymers Complex in Qatar
Feb 12 – Qatar Energy and Chevron Phillips Chemical recently celebrated the commencement of construction of a 6 billion-dollar integrated polymers complex in Ras Laffan Industrial City, Qatar.
During the groundbreaking event, His Highness the Amir of the State of Qatar Sheikh Tamim bin Hamad Al Thani laid a ceremonial foundation stone. Executives from Qatar Energy, CP Chem and its owner companies, Chevron U.S.A. and Phillips 66 Company, attended the ceremony. The 435-acre project site will include an ethane cracker with a capacity of 2,080 KTA of ethylene, making it the largest ethane cracker in the Middle East and one of the largest in the world. It will also include two high-density polyethylene derivative units with a total capacity of 1,680 KTA.
The facility is designed to use modern, energy-saving technology, which along with other measures, is expected to result in lower greenhouse gas emissions intensity than similar global facilities. The polyethylene units will use CP Chem’s Martech loop slurry process to produce high-density polyethylene, which will be primarily targeted for export from the state of Qatar.
The project is being developed by a joint venture company owned 30 % by CP Chem and 70 % by Qatar Energy. CP Chem is providing project management services to oversee the engineering, procurement and construction of the facility. Site preparation began in June 2022, and startup is expected in late 2026.
Honeywell Partners with Green Solutions for Vietnam’s First Green H2 Plant
Feb 22 – Honeywell has signed a Memorandum of Understanding (MOU) with The Green Solutions Group Corporation (TGS) on the Tra Vinh Green Hydrogen project, Vietnam's first green hydrogen plant in the Mekong Delta. Honeywell will bring to the project its ready now technologies such as project automation design and management, and energy management for energy transition, including battery energy storage systems (BESS), to enable TGS to integrate renewable energy sources into the green hydrogen plant.
"Honeywell's battery energy storage system will play a key enabling role in the Tra Vinh Green Hydrogen project," said Ramanathan Valliyappan, Regional General Manager of Honeywell Process Solutions. "It will extend renewable energy from TGS's solar farms beyond sunlight time as well as extend wind power when the winds are calm. Honeywell's BESS platform helps decrease costs and carbon emissions by providing grid stability from renewable power sources, thus enabling the production of green hydrogen at the Tra Vinh plant."
In addition to BESS, Honeywell will provide extensive solutions and expertise covering the entire hydrogen value chain to help TGS operate safely, profitably, and meet its renewable energy production goals.
Carbios, De Smet to Develop World's First PET Biorecycling Plant
Feb 27 – Carbios and De Smet Engineers & Contractors (DSEC), a world-class provider of Engineering, Procurement and Construction services in the biotech’s and agro-processing industries, jointly announce their collaboration to spearhead the construction of the world's first PET biorecycling plant.
Under the agreement, De Smet has been entrusted with the project management and detailed engineering, including procurement assistance and Carbios partners’ management, to ensure the execution of the plant's construction in Longlaville, France, due for commissioning in 2025. Carbios’ first commercial facility will play a key role in the fight against plastic pollution by offering an industrial-scale solution for the enzymatic depolymerization of PET waste to accelerate a circular economy for plastic and textiles.
Carbios' technology enables PET circularity and provides an alternative raw material to petro-sourced monomers, allowing PET producers, waste management companies, public entities, and brands to have an efficient solution to meet regulatory requirements and fulfill their own sustainability commitments.
The plant will have a processing capacity of 50,000 tons of post-consumer PET waste per year (equivalent to 2 billion colored PET bottles, 2.5 billion PET trays, or 300 million T-shirts) and will address waste with little or no value to date such as colored PET bottles, food trays, and textiles.
Linde Engineering, Yara to Develop World-Scale Coastal CO2 Liquefaction Plant
Feb 29 – Linde Engineering has signed a contract with Yara to build a world-scale carbon dioxide (CO2) liquefaction plant in Sluiskil, the Netherlands. The Sluiskil project forms a key part of Yara’s clean ammonia initiative, in which each year 800,000 tons of CO2 will be captured, liquefied, loaded onto special ships, and then subsequently locked away permanently below the seabed off the coast of western Norway.
The CO2 liquefaction plant will be built on-site next to Yara’s existing ammonia plant. After start-up in 2026, it will be a part of one of the first commercial carbon-capture storage (CCS) ventures in Europe. Recovering CO2 and injecting it into deep geological storage repositories is an important measure to reduce global warming caused by fertilizer production, which is inherently hard to abate.
The plant to be supplied by Linde will prepare the CO2 from Yara's ammonia plants for transportation. This will be achieved through processes including compressing, drying and liquefying using a refrigerant. The liquid CO2 will be stored in horizontal tanks with a total storage volume of about 15,000 m3, before shipping for sequestration. As the CO2 source is not connected to the final storage location by pipeline, the processing and liquefaction of the CO2 by a corresponding Linde plant make economical transport possible in the first place – in general possible by ship, train, or truck.
(ID:49948814)