The unsung heroes of the glass industry are glass furnace refractories, which are essential to maintaining the effectiveness, robustness, and security of high-temperature procedures. The cost of refractory materials typically makes up a sizable amount of a glass furnace’s budget.
The life of each refractory lining is extended by glass melting kiln hot repairs, which considerably lowers the lifetime costs of refractory materials. Even while these repairs require some degree of disruption to production operations, these outages typically have a brief duration since they avoid the need for time-consuming furnace cooling-down procedures.
Types of Glass Furnace Refractories
Bricks made of silica Bricks made of silica are renowned for having low thermal conductivity and a strong resilience to heat shock. Because they can endure the high temperatures and chemical reactions of the melting process, they are frequently utilized in the bottom, sidewalls, and crown of glass furnaces.
- Cast Refractories: The process of making cast-cast refractories involves melting raw materials and letting them set in a mold. They are highly prized for their remarkable ability to withstand corrosion and glass erosion, which qualifies them for usage in crucial glass furnace regions.
- Insulating Refractories: These are perfect for walls, ceilings, and oven doors because they minimize heat loss. They contribute to energy efficiency and help keep the glass furnace temperature steady.
- Refractories AZS — Alumina-zirconia-silica, or AZS, refractories are made of a combination of alumina, zirconia, and silica and have a great resistance to corrosion and high temperatures. They are perfect for covering surfaces like glass melting tanks that are in direct touch with molten glass.
Installation
Select refractory materials that work well with the temperatures and procedures used in your particular glass furnace. It’s crucial to layer refractories correctly. Taking into consideration elements like chemical interactions and thermal expansion, different refractories can be used in different parts of the furnace.
When mixing refractories and getting them ready for installation, according to the manufacturer’s instructions. To achieve the best results, consistency and appropriate curing are necessary. To guarantee the exact fit and bonding of refractories, installation calls for skilled workers and specialized equipment.
Basics of Maintenance
Refractories for glass melting kilns are the foundation of safe and effective glassmaking processes. Optimizing the lifespan and functionality of your glassware furnace requires selecting the right refractory materials, making sure the installation is done correctly, and putting regular maintenance procedures into place. Maintenance is the key to the smooth working of any hardware equipment. Here are a few key tips for regular maintenance schedules:
- Regular Inspection: It’s better to look for wear, erosion, or damage signs with routine inspections. To stop things from getting worse, find immediate solutions.
- Replacement of Refractories: Refractories deteriorate with time as a result of exposure to high temperatures and chemical reactions. To prevent unscheduled downtime, schedule refractory replacements.
- Repair: Refractory mortar or other repair supplies can be used to patch up minor crevices and cracks. More serious damage might need to be replaced or repaired by skilled professionals. This could avoid sudden breakdowns and other damages.
- Cleaning Procedure: To avoid blockage and preserve the effectiveness of heat transfer, periodically clear the accumulation of debris, ash, and glass from refractory surfaces.
Be Carefree
Glassmakers can minimize maintenance expenses and produce consistent, high-quality outcomes while avoiding downtime by knowing the many types of refractories that are available and adhering to best practices. To get a better idea about what suits your enterprise try to visit a couple of manufacturers in your neighborhood. Discuss the doubts and clarify any confusion regarding various aspects of the glass furnace. After getting a basic picture of what to choose you can select better products for your business.
Hy I'M Vivek kamani In Blogger
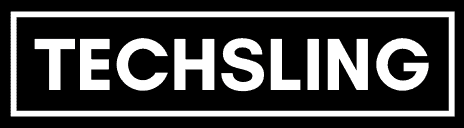