A big, bubbling cauldron of corn syrup sounds like an unlikely weapon against global warming. But Gaurab Chakrabarti and Sean Hunt think it holds the key to a new carbon-neutral way of making everyday chemicals for households and industries.
Greening the chemicals industry would go a long way to reducing global greenhouse-gas emissions. Chemical manufacturing accounts for a third of the carbon released into the atmosphere each year—mostly petroleum processing, which emits 1.5 billion metric tons of carbon per year.
Chakrabarti had an epiphany in 2015 while he was doing research on novel treatments for cancer at the University of Texas Southwestern Medical Center (he holds an M.D. and a Ph.D). He was studying enzymes—chemicals produced by all living creatures to speed up chemical reactions in their bodies—when he started thinking about how enzymes could be engineered to speed up chemical reactions in industrial processes. He wondered, in particular, if enzymes could make chemicals without troublesome byproducts such as carbon dioxide.
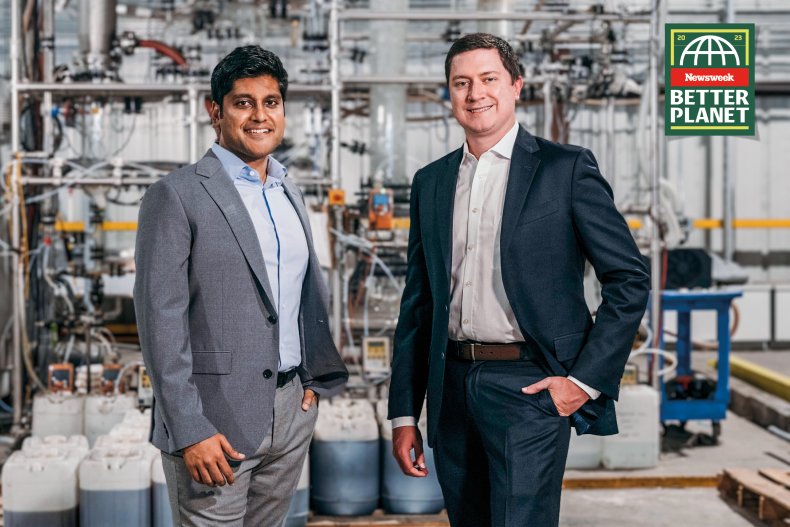
A year later he teamed up with Sean Hunt, then a chemical engineering graduate student at the Massachusetts Institute of Technology, to develop a way to make industrial chemicals with environmentally friendly ingredients like corn syrup, instead of the often environmentally harsh and climate-disrupting ingredients in the manufacturing processes currently used to make those chemicals. Together, they founded Solugen.
"We use systems that have been in nature for millions of years," says Chakrabarti, the company's CEO. "We just needed to create an environment where it could happen more efficiently." With a combination of conventional chemical engineering and bioengineering knowhow and a heavy reliance on artificial intelligence to design new biomolecules, Chakrabarti and Hunt came up with the "bioforge"—a 60-foot-tall tank that houses harmless ingredients like sugars, subjects them to biochemical reactions, and aerates them with a dense stream of microbubbles.
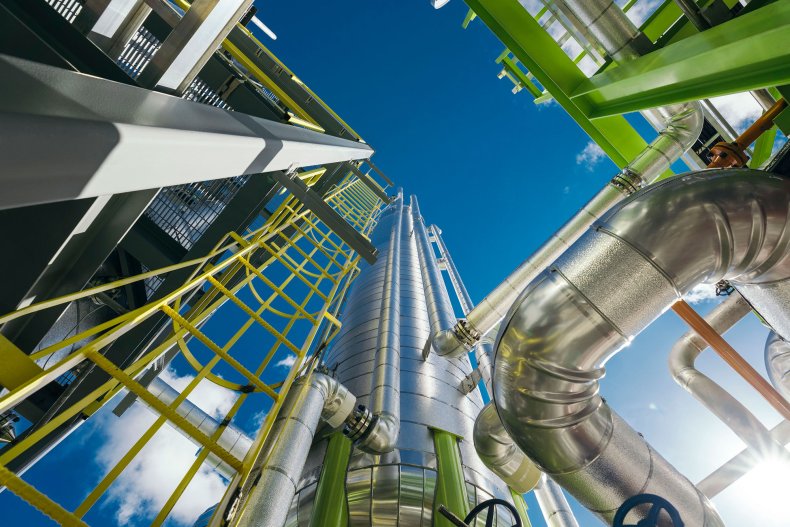
Today the bioforge can, in principle, produce a vast range of industrial chemicals and some new ones that work as well or better at certain tasks than those now commonly in use. For example, phosphates, currently widely used around the world in water-treatment systems to reduce corrosion, also cause aquatic-life-killing algae blooms. Solugen's biomolecule alternative, which the company is manufacturing in industrial quantities, is equally effective against corrosion but breaks down afterwards into harmless constituents. Other chemicals that the company is already manufacturing can be used in concrete production, cleaning and agriculture. And the company is planning to start manufacturing polymers and other chemicals that are widely used throughout the clothing and automotive industries.
Not only are the bioforges emissions-free, but the plants run on renewable energy, making Solugen's operations carbon-negative—that is, they actually remove more carbon from the environment than they put into it. Equally important, says Chakrabarti, the 10,000-gallon bioforge can produce the chemicals at enormous volumes, and do so profitably. Two 500,000 square-foot factories in Houston are churning out well over 10,000 tons per year of chemicals,and a third one is scheduled to go live this year in the Midwest. To pay for this expansion, Solugen has raised more than half a billion dollars from private investors.
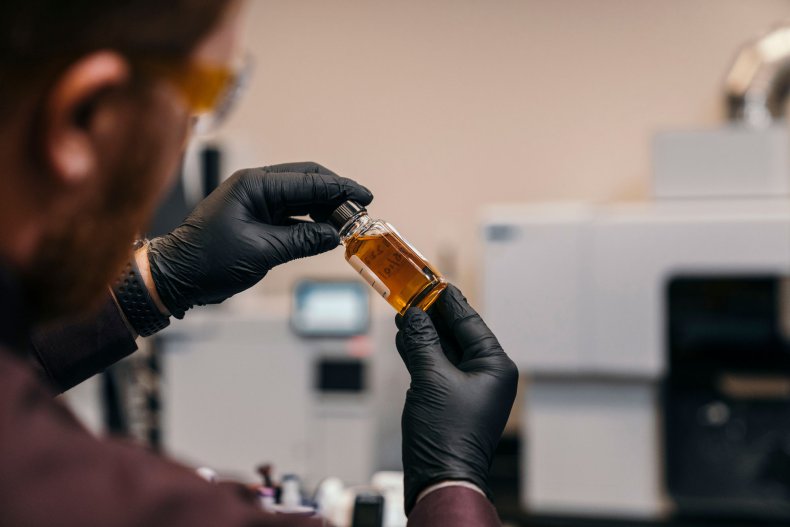
"We're creating a chance for the complete decarbonization and defossilization of the chemicals industry," says Chakrabarti.
Chakrabarti envisions bioforges becoming available in a wide variety of sizes and functions, perhaps by manufacturing them, or licensing the technology to others. These forges would run automatically, so that everyone in the industry from chemical giants to tiny shops will operate them. The biggest challenge right now, he says, is simply educating chemical buyers about the need to switch from their tried-and-true but carbon-intensive chemicals to greener, bioforged alternatives. "There aren't enough incentives in place at the moment," he explains. "But the regulatory environment is changing, we expect to see those incentives coming in."
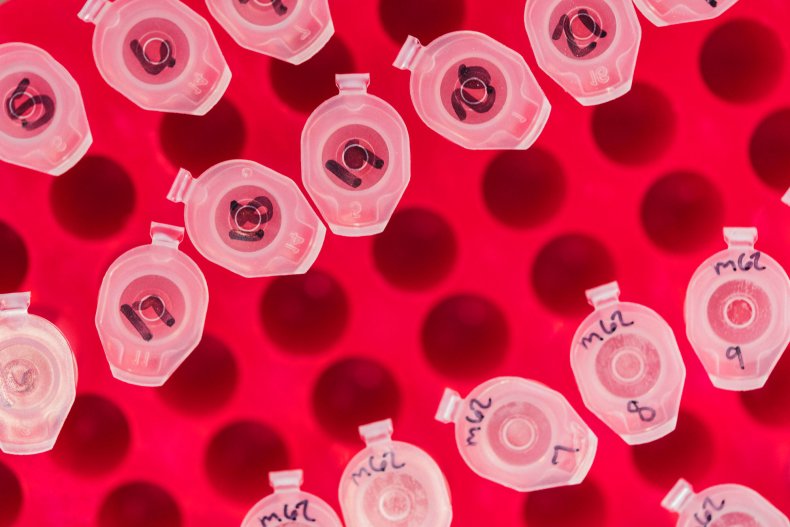
The company's goals over the next seven years are to reduce the carbon emissions released by industry into the environment by an amount equivalent to eliminating 2 million cars, and to make enough bioplastic to get rid of 5 billion non-degradable plastic bottles. It's just a matter of keeping the corn syrup flowing.