Next-Gen Solutions New AI-Powered Technologies
Related Vendors
Sea Vision presented its latest AI-powered technologies at the recently held Interpack fair in Germany. The firm focused on solutions across its three business divisions – machine vision, traceability and process automation.
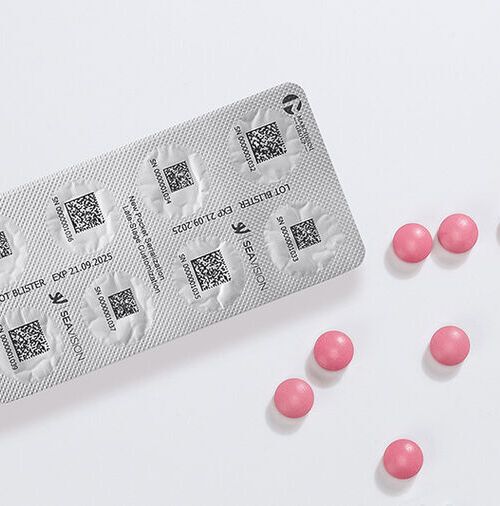
The Interpack fair was held from 4 to 10 May and was a particularly important edition for Sea Vision Group. The tradeshow week was the occasion to show the public, at stand A32 - Hall 15, the work of recent years in terms of the evolution of technologies for the Company's three business divisions: machine vision, traceability and process automation.
There was a particular focus on the new revolutionary technology powered by Artificial Intelligence algorithms developed with Argo Vision and applied to lipstick inspection and automated line clearance processes. At the fair, customers saw these technologies for real and enjoyed a hands-on experience of how AI can shape the pharmaceutical and cosmetic manufacturing processes of the future.
In traceability, the main focus was on the blister track & trace software (installed on the Marchesini Group blister packaging line - Hall 15, Stand A42 1-6) performing the in-line printing of serialized artworks on primary packaging, together with complete aggregation up to pallet level.
Technologies on show
Sea Vision continues its journey in the development of software applications based on Artificial Intelligence technologies, with the aim of strengthening and improving the range of inspection solutions for pharmaceutical products on which the company's history and expertise are based.
AI-powered Automated Line Clearance: Smart Clearance
Everybody knows that line clearance processes are crucial stages before production start-up. The aim is to ensure that equipment and work areas are free/clean from any residual material or document. However, these very important phases still require manual intervention by operators to perform specific paper-based tasks and activities, with the consequent risk of human error. The need for greater safety and smoother processes is what drives Sea Vision's Smart Clearance technology. This brand-new solution is driven by AI algorithms to automate line clearance procedures while avoiding errors, reducing the time needed and boosting the OEE of production lines.
As part of the yudoo 4.0 software suite, Smart Clearance Technology is capable of performing an automatic, accurate inspection of the packaging line work areas using cameras and sensors, highlighting anomalies and providing visual feedback for the operator in real-time, states the company. The system was demonstrated on a Marchesini Group RLF800 high-speed rotary labelling machine, which featured new complexities compared to the previous machine shown at the Achema exhibition, thus taking a step further in technological innovation.
In fact, the software integrates important new advanced automation features for the management of line clearance operations even on machines with articulated mechanical configurations such as RLF. Smart Clearance can now coordinate the movement of mechanical machine assemblies that stand between the cameras and the parts to be inspected. One immediate advantage is the ability to use a small number of cameras without the need to install more to capture all the hidden scenes, adds the firm.
The system is enhanced by AI algorithms and overcomes traditional limitations in terms of reflections, shadows and different lighting conditions.
yudoo 4.0 software suite
It is not possible to talk about Industry 4.0 without mentioning yudoo, a 4.0 platform that links automation devices, machines, IT and control systems together to manage the entire pharmaceutical production process and, at the same time, collect and analyze data to turn manufacturing insights and traceability insights into action and drive results in terms of OEE improvement.
In its full version, yudoo includes features for managing production lines, integrating existing Track & Trace architecture for serialization management, real-time OEE performance analysis, and evolved KPIs based on Business Intelligence tools, mentions the company. What does all this mean? Simple: yudoo is the pharmaceutical software suite that makes digital transformation a reality.
From blister to pallet: the next level of serialization and aggregation
At Interpack, the firm presented the Blister Track & Trace technology for the inline serialization of primary packaging and aggregation up to pallet level.
The solution was installed on the complete blister packaging line at the Marchesini Group's stand, including the full line from blister to casepacker-palletiser. The novelty lies in direct on-line printing via an on-board printer installed on the Integra 720, a solution that complements the off-line printing presented last year, opines the firm.
The system manages in-line printing directly on blister, together with the inspection of codes, and then automatically aggregates with the codes printed on their carton, cases and pallet labels.
Sea Vision and Marchesini Group decided to invest in this challenging project in order to further enhance product identification, which is a prerequisite in the healthcare industry. While, today, this condition is met for cartons and pallets, it does not apply to primary packaging such as pharmaceutical blisters. The aim of the solution is to fight the risk of counterfeiting when it comes to the primary packaging of drugs and to maximize investments already made by pharma companies to ensure that secondary packaging is traceable for 100 % safety during the distribution of products along the supply chain.
A new User Interface
Sea Vision has completely re-designed the user interface of their vision systems to improve user experience and usability, and presented it at Interpack. The main strengths of the new UI are web-accessibility, an app-specific interface and customization, shares the company.
- Web-accessibility enables multiple visualizations of the interface from a web browser from every device;
- App-specific interface: a specific skin is designed for each application (depending on the product – blister, syringes, track & trace and others...) but is based on the same software core. The app interface shows only what is relevant to that product, speeding up the operator's day-by-day activities, affording better ergonomics, usability and ease of use;
- Customization makes it possible to include specific customer personalization, such as showing specific data in a specific position, or customized dashboards;
- New menu organization divided into main sections: “desk” for configuration of the vision system; “run” for batch execution; “view” for visualization of dashboards and important batch information, and “BI” for the Business Intelligence data analysis.
Other systems on show
On several packaging machines at the Marchesini Group stand, customers saw many of Sea Vision's vision systems applications in action for various inspection needs. Examples include:
- presence of vials in tray and label presence – performed by the vision system Harletray, installed on a thermoforming machine;
- presence of imperfections inside or outside the bottle cap performed with Databox, and dimensional control of oral solids made with Harle2D|3D software – performed on a counting machine;
- control of cartons and leaflet codes performed by a Databox system on a standalone cartoning machine and on a stickpack line;
- check of the sku code correctness and variable data printed on the product label and label presence control – performed by the OCV multi system on a labelling machine for auto-injection devices;
- inspection of 2D sku code, label position on inhalers, and character control, performed by Databox installed on a labelling machine for round containers.
(ID:49464305)