Revised API 2350 Safety Standard for Petroleum Storage Tanks Reducing the Risk of Overfills — What you Should Consider Now
Related Vendors
The fifth edition of the API 2350 safety standard relating to large non-pressurized, above-ground petroleum storage tanks contains some significant changes. This article shows how these changes contribute to easier implementation of solutions to prevent overfilling, leading to enhanced plant and worker safety.
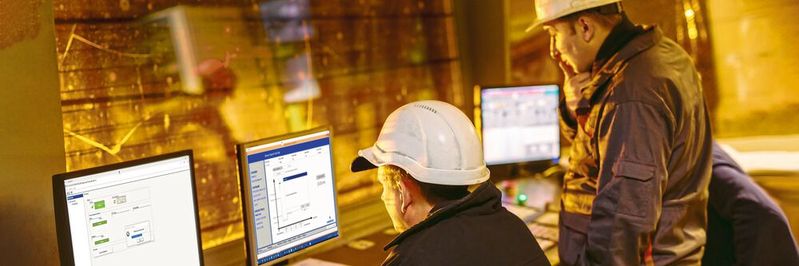
The American Petroleum Institute’s API 2350 standard is one of the key global standards that relate to overfill prevention. It provides minimum requirements to comply with modern best practices in the specific application of large non-pressurized above-ground petroleum storage tanks. API 2350 was created by and for the petroleum industry, with contributions from a wide range of industry representatives, including tank owners and operators, transporters, manufacturers and safety experts. It is aimed at owners and operators of fuel distribution terminals, refineries, chemical plants, and any other facilities that receive petroleum or chemical products into storage.
API 2350 was written from an international perspective, and is valid and applicable worldwide. The intention was not that it should compete against other safety standards, such as the International Electrotechnical Commission’s IEC 61511 standard, but instead that it should complement them.
Assessing the Risk of Overfills
The science of assessing risk comes down to one basic formula: risk = consequence × probability. Risk assessment is a cornerstone of modern overfill prevention because it creates awareness of hazards and risks, identifies who or what may be at risk and the potential cost of an incident, determines whether existing risk reduction measures are adequate, and prioritizes risk reduction activities.
A risk assessment is not a guarantee of zero accidents. However, tank overfills are predictable; risk assessment is a necessary tool to determine which protection layers should be implemented and how they should be designed and managed over time. When an overfill prevention system is used to reduce risk, the risk assessment determines the required safety integrity level.
API 2350 requires the use of a risk assessment system, with each tank having a risk assessment performed to determine whether risk reduction is required. The standard does not prescribe exactly how an organization should go about performing a risk assessment at its facility. However, the fifth edition includes three new very informative annexes, which provide guidance to owners and operators. These are:
- Annex E — An informative overview of risk assessment techniques;
- Annex F — Considerations at the transporter/owner interface (transfers); and
- Annex G — Informative description of categorization of tanks for a risk assessment.
Organizations may choose to use this method of categorization for risk assessment, which elevates the Annex to become a ‘normative’ requirement as part of the fifth edition. It should be noted that the fifth edition has introduced a category 0 classification, which is for tanks with manual hand gauging only.
Organizations that adopt API 2350 must establish or validate tank operating parameters. These include knowledge about tank categories, levels of concern (LOCs), alarms, alerts, automatic overfill prevention systems (AOPS), and attendance type. In the fifth edition of the standard, Annex D provides a detailed approach to determining these parameters, thereby helping organizations to achieve compliance.
Alerts, Alarms and Safety Areas Applicable to Each Tank
API 2350 outlines several LOCs, which are liquid level positions set by an organization for alerts, alarms and other AOPS functions. Defining these positions correctly for each tank at a facility is a critical aspect of overfill prevention, as it enables potential problems to be identified before an overfill happens. The highest of these LOCs is the critical high, which is the liquid level at which an overflow or damage can occur. Below this is the high-high alarm, for when the level is approaching critical high. This is the only alarm required by API 2350, and the AOPS level will be set at or above this point. Next down is the maximum working level, which is the highest level to which a tank can normally be filled. An alert may be used at this level if the operator chooses.
API 2350 fifth edition requires default minimum response times — i.e. the time required to detect an LOC, trigger an alarm and stop filling. These response times vary depending on the category of tank concerned. The standard also requires a liquid level safety margin of no less than 75 mm (3 in.) between two LOCs, for example the critical high and the high-high. A further requirement is that according to the OPP, all LOCs must be periodically reviewed and updated. Any changes to LOCs should undergo a management of change process, which is part of the overfill management system.
Modern Digital Wireless Networks are Permitted
Wireless technology has been deployed widely for measurement applications in process plants, but its use within safety functions has not been permitted. API 2350 recognizes that, while overfill prevention should be a priority for tank owners and operators, high installation costs due to lack of wiring infrastructure at many facilities can be an economic barrier.
The fifth edition points to the use of modern, digital wireless networks as an acceptable means of deploying overfill prevention utilizing the International Electrotechnical Commission (IEC) and International Society of Automation (ISA) network standards now widely available from major device manufacturers.
Proof Testing of Important Sensors and Systems
API 2350 does not address which equipment or technology should be used in overfill prevention. However, a large portion of the standard is devoted to procedures that ensure the correct ongoing operation of the equipment. These procedures include proof-testing (or verifying) the important sensors and systems in the overfill prevention safety loop.
The importance of proof-testing cannot be over-emphasized. When systems such as tank alerts, alarms or AOPS fail, the failures are for the most part unrevealed. This type of failure is referred to as a dangerous undetected failure. Great advances have been made in terms of self-diagnostic functionality available within level sensors and automatic tank gauging systems. This enables monitoring of many of the failure modes and the output of a diagnostic alarm in such cases, although no system has a 100 percent probability of diagnosing system faults. The only way to positively find all potential dangerous undetected faults is to proof-test the entire loop from the sensor to the final output (sensor, logic solver and final element or valve). It is recommended that the proof-testing requirements specified for AOPS are also applied to all alarms.
API 2350 fifth edition now requires all components involved in terminating a receipt to be proof-tested at least annually, unless otherwise supported by a technical justification (i.e. a calculation of the probability of failure on demand). Varying types of sensors are discussed in Annex C, with differing testing procedures associated to each type. Annex H provides owners and operators with informative considerations when deciding on a proof-testing regime.
Significant Benefits in Day-to-Day Operations
Adopting and implementing processes and procedures according to the API 2350 standard is a significant challenge, but is essential to mitigate the potential risk of an overfill due to failed equipment or human error. Although the main purpose of API 2350 is to help organizations increase safety by preventing overfills, applying the standard can also lead to other significant benefits in day-to-day operations, including improved operational efficiency and increased tank utilization.
Operational benefits may result from simplified and clarified alarm responses, improved operator training and qualification, better procedures for both normal and abnormal conditions, and enhanced inspection, maintenance and testing practices.
(ID:49217952)