:quality(80)/images.vogel.de/vogelonline/bdb/1845500/1845581/original.jpg)
Artificial Intelligence in Process Automation Use AI to Make Process Automation Relevant to Business Drivers
In the past, “more is better” often applied to process optimization – companies sometimes invested considerable effort to keep all processes in the optimal range and suppress every disturbance. But not all anomalies in processes are equally relevant to the profitability of a plant. With artificial intelligence (AI) methods, events can now be directly evaluated for their business relevance, thus opening up new possibilities for companies in the economic optimization of processes.
Related Company
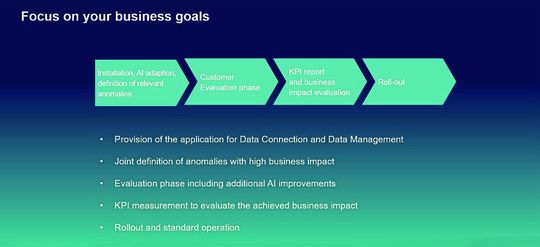
The aim of the AI-supported methodology is to provide plant operators with clear recommendations for dealing with anomalies and to be able to quickly identify process events that have a major impact on economic parameters such as productivity, availability, and quality. Performing this type of evaluation based on process automation data has not been possible so far. Although anomalies can be detected on the basis of process data, the extent to which an anomaly poses business risks, and how great these risks are, depends on the specific production and market conditions.
Evaluating Information in Context
A simple example shows how different this assessment can be. In crude oil production, large amounts of sand can reduce the service life of pumps. In this case, the operator of the production station can decide to protect the pump by reducing the flow rate or distributing it to other pumps until the sand has settled at the production point. This makes economic sense if the flow rate or value of the oil produced is low compared to the cost of repairing or replacing the pump. Conversely, if the flow rate is high and the value of the oil pumped is comparatively large, it may make more economic sense to continue to operate the pump despite the sand, since the expense incurred due to faster wear is offset by the higher pumping yield. Until now, this evaluation was the domain of the operator, who used their experience to estimate the impact of anomalies on the economic viability of the process.
Modeling for Impact Assessment
But what happens if the market environment changes or processes need to be able to produce for different markets – for example, both low-cost and high-value products for different orders? In this case, evaluating disruptions and events becomes much more complex. The same applies to networked causalities, for example, when energy consumption, productivity, and product quality all influence each other. Here, the economically optimal operating point of a plant can no longer be calculated simply on the basis of individual parameters but must be determined using process modeling.
The physical models used in this process have a weak point, though: they are based on a given plant condition. Changes in plant behavior – for example, due to aging – must be continuously updated. If the change is then reversed – for example, by a repair – the model must also be restored to its original state. This model maintenance involves considerable effort.
This challenge can be addressed with models that use artificial intelligence methods to detect and evaluate anomalies. The underlying algorithms are continuously trained during plant operation and thus learn to recognize new anomalies – but they can also reproduce previous states. This cumulative learning represents one of the key differences between AI-based and classical process models, and offers the advantage that the model can incorporate different plant states much more flexibly. In addition, an AI-based model can also make predictions about the outcomes of complex processes by correlating different connections and thus, for example, recognizing in good time when anomalies presage a plant failure.
Anomaly Detection With AI
There are now various solutions and providers for AI-based anomaly detection in process plants. However, in order for the AI to really be able to detect and evaluate business-relevant anomalies, the algorithms must not only be trained on the basis of process data but must also be focused. In other words, they must learn which anomalies have an impact on the profitability of the plant and which do not. For its AI Anomaly Assistant app, Siemens has developed a methodology that demonstrates how such a training and focusing process can be applied to industrial processes.
First, the process data that will be used to train the app must be recorded and collected. For this purpose, the data are transferred from the process control system to the customer-specific instance of AI Anomaly Assistant via a defined interface for evaluation. This ensures that the data can always be used in the same format for evaluation, regardless of the type of collection.
Then the first step in the AI training process begins. In this step, the data analysts at Siemens generate anomalies from the process data and cluster these anomalies based on rough process information. The results are then discussed with the plant operator to filter potential anomalies according to their relevance. This step is particularly important, as not all detected anomalies are actually relevant to the process and business.
Based on the feedback from this phase, the AI is trained again to become more focused so that it only detects the anomalies identified as being relevant. In addition, the experts at Siemens also use the user feedback to identify those anomalies that have a high probability of being business-relevant, based on their impact on performance indicators such as availability, yield, or quality.
This pre-selection of high-relevance anomalies serves as the foundation for refining the AI focus by the plant operator. During this stage, the application supports the operator with a dashboard in which anomalies can be commented on, evaluated, and selected. This evaluation phase is accompanied by several feedback loops, so that in the end the plant operator receives a well-trained and focused AI that is able to evaluate anomalies for their business relevance based on the process data.
AI Relies on Process and Product Know-How
The selection and quality of the process data is just as relevant for the AI as choosing the right parameters for evaluating the anomalies. This is why Siemens has established a structured approach to implementation and training. This ensures that the know-how of process experts and data analysts both contribute to the implementation process and results, and that the application meets expectations and requirements. This process also needs to leverage the expertise of the plant or process operators, as they are the authority for identifying bottlenecks or issues in their processes that cannot be resolved with conventional methods, and which key data from the processes are decisive for business success.
However, especially with sensitive processes, it is important that proprietary and/or confidential product and process data be protected. And here, too, AI-supported modeling offers an advantage over classic process modeling. Use of AI allows process data to be generalized and anonymized to a greater degree, since the relationship between the data is generated by the model itself. To assess anomalies and focus the AI, data analysts need only basic information about the nature of the process, but not about the process details. Even the names of parameters can be largely anonymized. In this way, AI Anomaly Assistant ensures extensive protection of the plant operator’s intellectual property rights.
AI Is a Valuable Aid in the Business Environment
In this way, applications such as AI Anomaly Assistant can help companies improve the profitability of their processes and strengthen their competitive edge. At the same time, they can leverage a tool that learns along with their processes and products and is also able to use anomalies to prevent risks. The combination of cloud technologies, AI, and know-how covering both the application and the process ensures that AI-supported methods can be quickly and precisely adapted to the relevant requirements and business targets, while offering excellent protection of the plant operator’s intellectual property.
* The author is a product owner at Siemens AG in Erlangen, Germany.
(ID:47473502)