:quality(80)/images.vogel.de/vogelonline/bdb/1835800/1835822/original.jpg)
Article requires registration
Pump Technology What Will The Pump Design of The Future Look Like?
Shorter planning and construction times, more flexible utilization options through rapid modifications, and everything as energy-efficient as possible: The Enpro initiative (Energy Efficiency and Process Acceleration for the Chemical Industry) is opening up interesting options for the process industries with its various development projects. New designs for pumps also offer undreamed-of opportunities, as the first modular concepts and the Hector project show. We explain how tomorrow’s pumps may be both modular and energy-efficient.
Related Companies
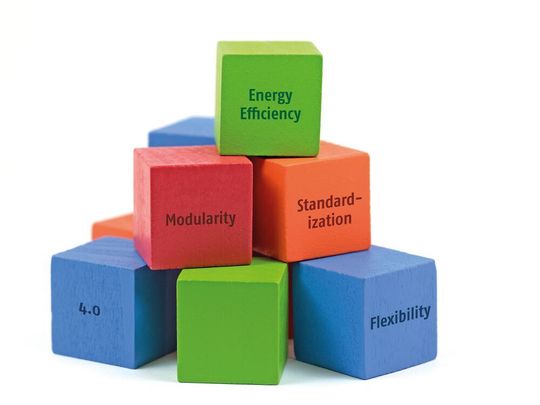
Pumps consume 30 percent of the electricity used by industry. Refrigeration systems, compressors and fans account for a further 34 percent. In total, therefore, rotating equipment consumes two-thirds of industry’s electricity. It’s thus no surprise that energy efficiency plays an important role in the Enpro initiative and enjoys great attention in the process industries. The same applies to the topic of process acceleration: Anyone who brings up the blessings of Industry 4.0 quickly comes to expect greater flexibility in production technology. To achieve this, systems must be easily and quickly convertible. In particular, new machines should be able to be integrated into the production process in an uncomplicated manner.
The Modular Equipment for Energy Efficient Chemical Production project aimed to use modular equipment to reduce project runtimes while improving energy efficiency in the chemical industry.
One approach to a solution is modularization, which is based on two essential points: process equipment must be subdivided into modules, and the technology used to automate it needs a modular structure. This means nothing less than a paradigm shift in process development — away from basic process operations and towards services provided by modules. When automating a stirred tank, for instance, instead of individually integrating the feed valves, the temperature control unit, the stirrer and the required sensors, the module instead has a kind of ‘printer driver’ known as a Module Type Package (MTP).
Sign in or register and read on
Please log in or register and read this article. To be able to read this article in full, you must be registered. Free registration gives you access to exclusive specialist information.
Already registered? Log in here