:quality(80)/images.vogel.de/vogelonline/bdb/1834200/1834299/original.jpg)
Pumps Pump Design of the Future
Shorter planning and construction times, more flexible utilization options through rapid modifications, and everything as energy-efficient as possible: The Enpro initiative (Energy Efficiency and Process Acceleration for the Chemical Industry) is opening up interesting options for the process industries with its various development projects. New designs for pumps also offer undreamed-of opportunities, as the first modular concepts and the Hector project show. We explain how tomorrow’s pumps may be both modular and energy-efficient.
Related Companies
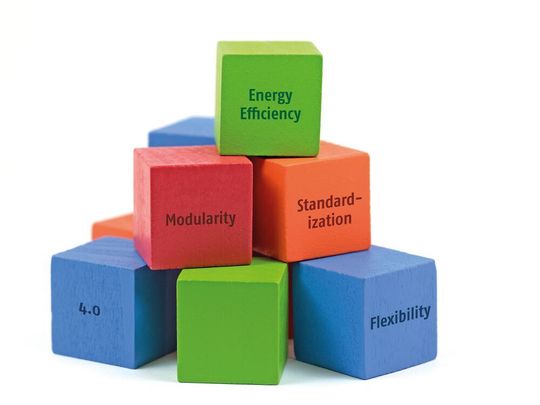
Pumps consume 30 percent of the electricity used by industry. Refrigeration systems, compressors and fans account for a further 34 percent. In total, therefore, rotating equipment consumes two-thirds of industry’s electricity. It’s thus no surprise that energy efficiency plays an important role in the Enpro initiative and enjoys great attention in the process industries. The same applies to the topic of process acceleration: Anyone who brings up the blessings of Industry 4.0 quickly comes to expect greater flexibility in production technology. To achieve this, systems must be easily and quickly convertible. In particular, new machines should be able to be integrated into the production process in an uncomplicated manner.
One approach to a solution is modularization, which is based on two essential points: process equipment must be subdivided into modules, and the technology used to automate it needs a modular structure. This means nothing less than a paradigm shift in process development — away from basic process operations and towards services provided by modules. When automating a stirred tank, for instance, instead of individually integrating the feed valves, the temperature control unit, the stirrer and the required sensors, the module instead has a kind of ‘printer driver’ known as a Module Type Package (MTP).
It’s not an impossible task: In cooperation with Wago and the Chair of Automation Technology at the Technical University Cologne, manufacturer Seepex presented an MTP-based pump module at the 2019 Hanover Fair. It can be imported into the automation systems of various manufacturers to provide services such as dosing and filling.
Enpro and the Pumps
The first phase of the initiative (Enpro 1.0) investigated the modularization of pumps. The Modular Equipment for Energy Efficient Chemical Production project aimed to use modular equipment to reduce project runtimes while improving energy efficiency in the chemical industry. The main objective was to demonstrate that a module-based approach enables the reuse of equipment blocks already designed in previous projects. Work at iPAT (University of Erlangen-Nuremberg, Chair of Process Machines and Plant Engineering, Prof. Eberhard Schlücker) within the scope of this project focused on the modularization of different pump types. Depending on the required process parameters, different pump types (e.g. centrifugal pumps, eccentric screw pumps, diaphragm pumps) achieve different good results in terms of energy efficiency. However, up to now there has been the problem that replacing the pump often involves far-reaching changes to the overall system. This begins with the fact that there is no uniform connection geometry for pumps (within the framework of Enpro, all the manufacturers taking part have therefore provided their pumps with a uniform connection geometry). In addition, different pump types also have different characteristics with regard to their pumping performance.
An important aspect that must be considered for interchangeability is pulsation, which is produced by different types of pumps to varying degrees. For this purpose, suggestions for improvement are being developed for the different pumps, specially adapted to their respective characteristics. The aim is to reduce the existing pulsations of the different pump types to a uniform minimum level.
A module-based planning approach was developed that aims to select and configure the most suitable equipment from a database, rather than designing it individually. In cooperation between chemical companies, engineering firms, software producers, equipment manufacturers and academia, the required modular equipment was designed. The versatility of the module is achieved by defining the main device as the core of the module, which is complemented by a variety of additional functions. An example of a main device can be a specific type of pump, while the piping required to flush the pump can be the configurable additional function. To make these equipment modules applicable to the design of chemical plants, an engineering tool has been developed that evaluates the function of the equipment in the process and its energy efficiency. It thus helps in the first step to select the most suitable and efficient main equipment. Additional functions are added In further steps. The modular equipment thus designed is used in an engineering tool for the entire planning process, from basic through to detailed engineering.
The approach was physically demonstrated on a variety of pumps with different operating principles. A monitoring system was developed to observe the dynamics of each pump’s operating state. The system is designed generically for any pump type. An innovative damper system was developed to ensure pulsation-free operation even for positive displacement pumps. Finally, a pump set will be developed whose economic connection dimensions are defined only by the volume flow delivered by the pump, regardless of the pump’s operating principle. All this together will allow quick selection of the most energy-efficient pump and, in addition, enable the replacement of pumps by more efficient models.
On the Trail of Wear and Tear
While the focus in Enpro 1.0 was on the individual modules, the Hector project (Highly Efficient Chemical Plants Using Technical Operations Research) focuses on their efficient interaction in the overall system.
The partner companies for Hector are Evonik (module design and maintenance using the example of pump modules), Lewa (experiments and models for wear and efficiency in reciprocating diaphragm pumps), Netzsch (a methodology for diagnosing and predicting wear in a progressive cavity pump), Klaus Union (modular centrifugal pumps and modular valves) and the engineering company IAV (soft sensors for diagnosing modules and predicting failures). The project is coordinated by Prof. Peter F. Pelz, TU Darmstadt; his colleague Philipp Wetterich has asked the partners about the state of affairs, which we report below.
The pump manufacturers involved focus conspicuously on wear behavior. The background to this is that a pump in a modular system is not specifically designed for the task at hand, and therefore is likely to be working beyond its best operating point.
Lewa
As a system and solution provider, Lewa has the role of component characterization in the project, as Dr Philipp Trunk (Project Manager Digital Innovation) reports. Over the course of the project, operating data must be collected and wear and tear characterized. In addition, there are questions of modularization, characterization of the construction program, and integration into modular plant technology and plant engineering processes. Lewa expects to increase the predictability of wear and damage in the future. This applies both to the newly developed pumps and to the retrofit of the existing portfolio. In addition, the interaction with Evonik as the operator and the other component manufacturers on the subject of modularization offers valuable implications for sensible standardization into a modular construction kit that has a good ability to integrate the pump subsystem into the overall plant. The supplier hopes that this will lead to broad acceptance of its solutions, especially among Lewa’s very important operator customers in the process industries. Last but not least, optimizing the system concept moves big levers for higher energy efficiency.
Klaus Union
Klaus Union Technical Manager Frank Holz states that the aim of his project is to allow pumps to wear out in a controlled manner, in order to be able to draw conclusions about the condition of real pumps later on. By monitoring pumps in the plant and the now known state of wear, it should be possible to minimize unforeseen pump failures and hence plant shutdowns. In the first step, Klaus Union systematically examines the influence of individual wearing components of the pump (e.g. wear ring, throttle ring, plain bearing) on the performance data of the pump in order to determine the particular influence of wear in this component. Performance data from new pumps forms the basis for this. In the second step, the influence of all the worn components on the performance data of the pump is determined by measurement. The aim is to obtain reliable conclusions about the performance data and thus the state of wear of the pump, while needing as few sensors as possible to be installed on the pump. For demanding customers, Klaus Union will also use the knowldge gained in these tests to offer new, more wear-resistant components.
IAV
To ensure efficient operation of the modules in the overall system in a cost-effective manner, the use of soft sensors is being investigated. Here, too, the focus is not on the individual module, but on the system-wide, targeted and redundant recording of system variables. The aim is to draw conclusions on the state of wear of the modules by resolving data-induced conflicts and to develop predictive diagnostic functions. The information gained in the project offers great potential for the energy-efficient (re)design of modular systems.
The aim is to develop methods for detecting wear — at both the pump level and the overall system level, says IAV Project Manager Patrick Stracke. This enables precise diagnosis of the defective components in the system network. IAV is using know-how from more than 30 years of experience as an international development service provider.
Netzsch
Eccentric screw pumps very often work in applications with high wear. In the future, Netzsch wants to offer its customers the possibility to monitor the wear condition of its pumps. This means, for example, that the next maintenance shutdown can be planned in good time. Hector is thus laying the foundations for introducing predictive maintenance for eccentric screw pumps on the basis of system-specific sensor data, says Mikael Tekneyan, Development Engineer Global Technology & Product Management. To this end, Netzsch has already run wear tests and made the data available for modeling.
Aiming to Cut Complexity
In the Enpro 1.0 initiative, case studies were used to show that computer-assisted, module-based design can significantly reduce engineering effort and project lead time for new plants. The reason for this is the reduction of complexity enabled by pre-selected modules. However, the reduction in complexity comes at a price: a plant created by combining a limited selection of modules will not be as efficient as one that is tailored to the application. To combine the advantages of the modularization approach with energy efficiency efforts, the modules available at the planning stage — the standard modular kit — must be selected carefully. On the other hand, further optimization potential must be tapped through a systems approach to planning and operation.
For the pump manufacturers, the wear of their pumps and the detection of this wear is of particular interest. But of course this also touches on the question of the energy they use. No matter how efficient it is, only a pump that is reliable in the long term can achieve low life-cycle costs.
* * The author is a freelancer for PROCESS. Contact: editor@process-worldwide.com
(ID:47354466)