:quality(80)/images.vogel.de/vogelonline/bdb/1834000/1834038/original.jpg)
Automation Device Replacement Made Easy?
What does the future handling of field devices look like? Why has digitalization in the process industry not yet progressed as far as users and manufacturers would like? The discussions around device management provide an insight into the challenges. Thanks to Profinet and APL, solutions for this are already starting to emerge.
Related Companies
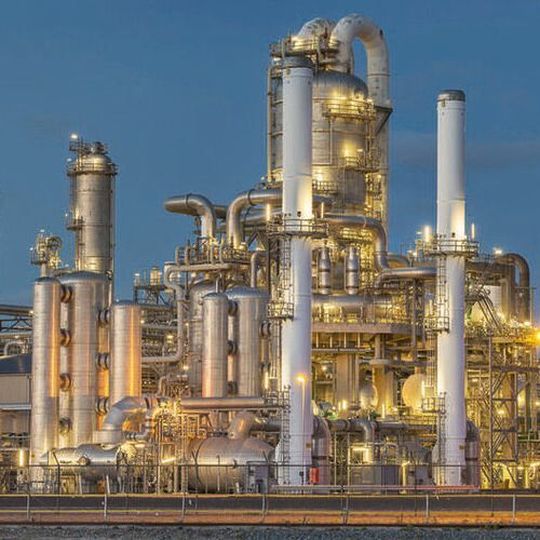
The simple replacement of field devices in process plants is still a tricky business — despite all the efforts made for intelligent integration technologies such as EDDL, DTM and FDI. In addition to assembly and connection, as well as requirements due to explosion protection, the documentation effort in particular is immense.
How can equipment management in the process industries be made easier? “The technology must be easy to implement, i.e. the complexity must be minimized or encapsulated,” says Sven Seintsch, head of the test laboratory at Bilfinger Maintenance and head of the Namur working group 2.6 Digital Process Communication. Standards and interoperability also play a major role, as does investment security. “Lifecycle concepts must cover a period of 10 to 15 years. Any technology we introduce today will most likely still be in the plant in 15 years’ time,” Seintsch notes with regard to the many existing plants in the process industry. Users must therefore see a clear benefit to introducing new technology, otherwise they will always act hesitantly.
To better understand the user requirements and show how these can be realized with the existing and future PI technologies (including PA Profile 4.0), use cases need to be described first. The Namur Working Group 2.6 and the PA Marketing Working Group of PI are working closely together on this to prioritize any gaps identified and include them in the PI specification work. To this end, Seintsch presents three examples under discussion that show how good device management can work in practice.
Use Case 1 — Commissioning
A PCT plant engineer would like to add an additional temperature measurement on a column. A free branch on the column is available. He selects a temperature sensor with transmitter and thermowell to suit the process conditions and the measurement task, and plans the change, for instance by creating a PCT measuring point sheet in the plant’s integrated engineering tool. After checking and releasing the change, the parameters relevant to automation (at least the profile parameters) are transferred from the engineering tool to the DCS/asset management by means of an interface according to NE150. The temperature probe can then be installed as soon as a work permit has been issued.
Use Case 2 — Configuration management
A PCT operations engineer and her support team (internal and external tradespeople, etc.) configure field devices on site or via mobile devices with Bluetooth, or remotely via a web interface or an engineering/maintenance station. Regardless of the tool selected, configuration parameters remain synchronized in all environments.
Use Case 3 — Easy device replacement
A PCE technician is called out at 2 A.M. to replace a defective measuring device that is essential for the continued operation of the system. A device that is equivalent (same measuring method, same materials and connection size, etc.) but not identical (different manufacturer, newer model) is in the warehouse. He installs the device and connects it. Now there are two variants that would be practicable: a) The system recognizes that it is an equivalent but not identical device. The unit is registered in the system with the login data of the original unit. The profile parameters stored in the engineering/maintenance station are then loaded into the unit and it is automatically commissioned with the basic functions. The PCT technician on site does not need any further personnel support in this case. b) By using the FDI (Field Device Integration) device package, the device is immediately visible and operable on the Ex tablet on site as well as on the engineering/maintenance station. It pulls all profile parameters and, after completing the configuration, makes at least the profile values (e.g. basic measurement and accompanying values) available for process control and saves the device with its parameter data in the system again. In both procedures, the unit can continue to operate after a restart.
Asking the Users What They Want
For these use cases to become a reality, some requirements must first be met, according to Seintsch. These include, for example, a clear manufacturer-independent commissioning procedure, but also a rule that profile parameters are created for all devices and system equipment, and implemented in the profile GSD across the board. These should be available via device profiles and be further developed in a downward-compatible manner. Very importantly, they need uniform semantics across different organizations.
Information on the unit status should also be available to the maintenance staff during operation. “Condition monitoring, an evaluation on unit failures, diagnostic information and newly commissioned units are important topics in unit management,” says Seintsch. In his opinion, device calibration could also be simpler.
Cooperation Paves the Way for New Technologies
There are already technologies that pave the way for this. To this end, PI has for a long time been cooperating with the OPC Foundation so that the OPC UA information models can be used in the PI technologies. PI has also been working with the Fieldcomm Group (FCG) for years. Here, an FDI solution was developed that works across organizations. Once an FDI device package is available for all field devices, new and old, device management becomes easier, especially if all host systems can also fully process the device packages and are certified accordingly. This ensures interoperability on both the device and the system side. The manufacturer-neutral OPC-UA interface must also be established in all systems with the NOA (Namur Open Architecture) information models.
For integration in IOT applications, the information model of OPC UA is used. The OPC UA for Devices specification already applied there is used for the Profinet mapping. Thanks to the TCP/IP channel, which has always been open in Profinet networks, OPC UA access can take place via the controllers, gateways or directly to subordinate devices. With OPC UA, the connection to superimposed levels is simultaneously realized via the second communication channel, so to speak, using the NOA principles.
Furthermore, Profinet allows other protocols to coexist in the network, e.g. to operate other devices or diagnostic tools in the same network without these having been explicitly designed for Profinet. The advantage is that Profinet is aware of these different networks and prioritizes the transmission of data accordingly. Last but not least, the device profile for PA Devices was also extended to Profinet in version 4.0. Among other things, this involved aspects such as simple device replacement or intervention in the system during operation.
Ethernet-APL (Advanced Physical Layer) is another key to a new communication infrastructure in the process area. This technology offers the potential to unify the infrastructure for both safety and non-safety applications. In contrast to the hierarchically structured system environments of today’s plants, Ethernet-APL allows unrestricted access to all process and device data, down to each individual field device. This data is thus available without restriction. The fact that this works is demonstrated by test facilities at BASF and Bilfinger Maintenance, where the first prototypes of devices with Profinet as the communication interface have been used by various industrial partners. The tests showed that Ethernet-APL is suitable as a physical layer in the area of process automation and as a basic technology for higher-level applications.
Outlook: By combining FDI, profile parameters and Ethernet APL, Plug & Produce Ethernet communication can be achieved in the field. This gives the user full transparency throughout the entire life cycle of the system. Furthermore, it offers minimum complexity and maximum economic efficiency if at least 80 to 90 percent of the field devices are connected via Ethernet APL. User Seintsch also confirms that in principle this is the right way to go, although there are certainly still a few questions that need to be clarified in detail.
* * The author is a freelance specialist journalist for chemistry and technology. Contact: PI Profibus & Profinet International: question@profibus.com
(ID:47356618)