:quality(80)/images.vogel.de/vogelonline/bdb/1831500/1831514/original.jpg)
Filling of Pharmaceuticals Filling the Gap: Reducing Commissioning Times for Pharmaceutical Filling and Packaging Lines
Due to the urgently needed capacities for vaccines, engineering companies and OEMs must react fast to increasing demand for aseptic filling lines. These lines are not only required for Covid-vaccines but also to fill the capacity gaps for other important pharmaceuticals and disrupted supply chains.
Related Companies
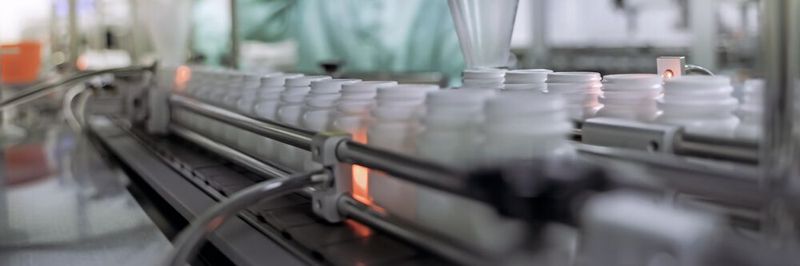
The mRNA formulations and highly potent drugs based on small molecules that are needed for vaccines and personalized drugs, demand a high degree of control and automation. Therefore, fully integrated systems, plug-and-play solutions and modular concepts are on the rise and can be brought online very quickly. This is also thanks to the connectivity and intelligence of complete turnkey solutions.
In a study, Markets and Markets, projects the global pharmaceutical packaging equipment market to reach $ 10.4 billion by 2025 from $ 7.3 billion in 2020, at a CAGR of 7.4 % from 2020 to 2025. The growth of the market is driven by the rapidly growing generic and biopharmaceutical markets, growth in OTC drug sales, rising need for flexible and integrated packaging equipment, increased offshore manufacturing in the pharmaceuticals market, and the introduction of regulatory standards on packaging and stringent norms against counterfeiting. The Covid-19 pandemic has largely impacted healthcare delivery globally since December 2019. Due to the coronavirus pandemic, the number of R&D procedures performed in pharmaceutical companies has increased significantly. Scientists and researchers worldwide are engaged in the development of vaccines and drugs for the treatment of coronavirus. This scenario is expected to have a direct impact on the pharmaceutical packaging equipment market.
For instance, Syntegon Technology, formerly known as Bosch Packaging Technology, has witnessed an increase in the sales of pharmaceutical packaging equipment due to the coronavirus outbreak across the globe. The company also showcased its latest process and packaging technologies at Achema Pulse in April. The objective was to emphasize on substantial and intelligent technologies for the pharmaceutical and food industries. “Pharmaceutical manufacturers are increasingly relying on shorter delivery times for their equipment,” says Stephan Hüttner, Head of Engineering Process Systems at Syntegon's Pharmatec product brand in Dresden. “Thanks to the SVP Essential’s standardized modular design, we can supply our customers with a fully automated, ready-to-use system in just six months.”Also, Syntegon has expanded its customer service activities and introduced new measures that include providing customer services through digital platforms and increased spare parts deliveries.
Engineering company GEA points out that despite the incredible achievements that have been made in terms of developing and delivering a number of approved and administered Covid-19 vaccines in recent times, governments, politicians and the general public alike are still questioning why it takes three to five years to bring a commercial-scale biopharmaceutical manufacturing plant to full operational functionality. GEA Group’s Heinrich Meintrup, Head of Pharma & Healthcare, believes that the key to significantly shortening this timeframe is modularization, digitalization and collaboration. By subscribing to a philosophy of standardization and modularization, a digitally enhanced project delivery process and keeping the number of interfaces to a minimum, significant gains can be made. “We have to make the best use of existing intelligent solutions,” advises Meintrup, “adhere to current standards and regulations, and focus on mutually agreed targets and incentives. Disruptions and delays can cost millions of dollars; but, by taking a smarter and leaner approach, GEA believes that the design, construction and qualification of pharmaceutical manufacturing plant and facilities can be accelerated, simplified and delivered with predictable outcomes in a shorter timeframe.”
Pharmaceutical manufacturers are increasingly relying on shorter delivery times for their equipment.
Collaboration Is Key
Another way to accelerate the construction of production and filling lines is the upgrade or extension of existing facilities. The Biontech biotechnology company based in Mainz has converted an existing facility in Marburg for the production of the Covid-19 vaccine in a record time with assistance from Siemens. The production plant has been producing the active substance since February and the vaccine BNT162b2 (also known as Comirnaty) since the end of March 2021. Biontech acquired a production facility for this in the fall of 2020 that was already equipped with capabilities for producing biotechnological substances. Through collaboration with Siemens and the team of experts on site in Marburg, the project timeline for converting the existing facility for the production of mRNA-vaccine was cut from around one year down to five months, whereby the implementation of key parts of the new Manufacturing Execution System (MES) was reduced to two and half months. The new system and end-to-end digitalization of production enable conversion to “paperless documentation of production”, which can immediately fulfill all documentation requirements.
Since the outbreak of the pandemic, Optima Pharma has also been making great efforts to adapt existing filling systems for vaccine filling and to build new filling systems with isolators as quickly as possible. “Our employees have been extremely challenged and are delivering top performance worldwide,” says Juergen Rothbauer, Managing Director of Optima Pharma. One example for a successful collaboration during the pandemic is with Thermo Fisher, headquartered in Waltham, Massachusetts.
The company’s Pharma Services business provides contract development and manufacturing services, which includes sterile fill operations for Covid-19 vaccines and other critical care medications for pharma companies globally. As a strategic partner with the necessary technological know-how, and end to end drug substance and drug product development and manufacturing capabilities, Optima is helping the company increase capacity for vaccine filling at several of its sites as quickly as possible.
As one of the companies from the Packaging Valley in Germany, Optima is also part of a strong network. Under to the motto #GemeinsamMehrErreichen (Achieve more together), companies from the Packaging Valley are developing new machines in record time, existing lines are adapted to the new requirements, delivered and put into operation with all the quality features. Suppliers, service providers and packaging machine manufacturers pull together. They develop and produce reliable, high-performance components and equipment for auxiliary products, diagnostic test kits and vaccines. And they do so within the shortest possible time. Whereas a project might take several months, the target is now set at just a few weeks. Fortunately, the companies from the packaging cluster in southern Germany had already set the course before the pandemic began. Many things are done digitally, such as commissioning or maintenance of the equipment at the customer's site. Some things, on the other hand, can be performed physically with worldwide networks.
Accelerated Development Times
Technologies from Syntegon Technology are used in the production of vaccines. This includes equipment for manufacturing vaccine substances and filling them into vials, as well as inspection machines for quality control. Thanks to the former Bosch packaging division's experience with biotechnological drugs, the technologies are also suitable for the new and highly sensitive mRNA vaccines. In addition, the company ramped up pharmaceutical services right at the start of the pandemic to accommodate the immense need for rapid maintenance and machine rebuilds.
Fast and safe filling of the sensitive substances is also guaranteed by Rommelag's cool BFS technology. The blow-fill-seal process is considered by experts to be one of the safest aseptic filling methods available. Rommelag is the only company in the world to have a BFS pharmaceutical production facility at its Swiss contract filling plant not far from Lucerne that is certified to Biosafety Level 2 (BSL-2) requirements.
The packaging of the small vials in cartons is handled by the systems from Harro Höfliger. Feeding, filling, sealing, labeling, quality control — all automatically. Here, too, fully automatic packaging lines are provided in multi-shift operation within a very short time. Markus Höfliger, Chairman of the Supervisory Board, emphasizes the importance of a network: “Without partner companies and a functioning supply chain, such a mammoth task cannot be solved in such a short window of time.” In addition, process technology from the company is used in the production of tests for the detection of coronavirus. Harro Höfliger also receives automation support from Heitec.
High performance and fast delivery of sensitive products make precise robot technology irreplaceable. Here in particular, undamaged storage and transport is more important than ever. PCA Roboter- und Verpackungstechnik delivers systems for the safe packaging and palletizing of so-called absorbers in a rush. They are used primarily in operating rooms to keep the air clean.
These are by no means all the projects that have sprung up overnight in the fight against the virus. Some key developments from the Packaging Valley and beyond include:
- In July 2020, Romaco Holding (Germany) launched Macofar’s Micro Robot 50. This product launch has strengthened the company’s filling machine portfolio.
- In February 2020, MG2 (Italy) and Pharm Alliance (UK) undertook a partnership to strengthen MG2’s presence in the French pharmaceutical market.
- In March 2019, Multivac established a new production facility in China to cater to the requirements of customers in China with even greater focus and speed to manufacture packaging machines.
- In June 2018, IMA acquired a 70 percent stake in Ciemme. This acquisition helped the company to broaden the portfolio of its end-line automatic cartooning machines.
(ID:47380458)