:quality(80)/images.vogel.de/vogelonline/bdb/1812500/1812570/original.jpg)
Smart Process Manufacturing Congress 2020 Digitalization: Myths and Insights
Is it time to dispel outdated notions surrounding the term “digitization?” — Speakers at the Smart Process Manufacturing Congress 2020, a virtual event organized by PROCESS, described a whole series of reservations or myths. The fact remains: Digitization is not a sprint, but a marathon — and sometimes even combined with a hurdle race. But it is also a fact that the benefits can be immense if tackled correctly.
Related Companies
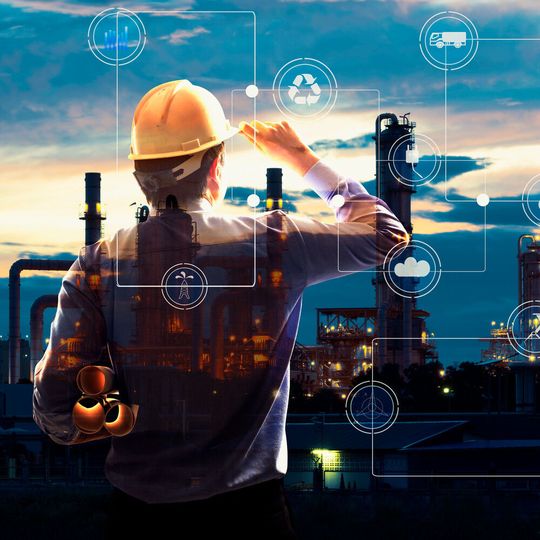
While the generation of digital natives probably think of knowledge-based systems such as IBM Watson or Google and chatbots when they think of “artificial intelligence”, the older generation is probably more influenced by the cult movie “2001: A Space Odyssey”, in which the supercomputer HAL is the secret star of the film. It develops an unpredictable life of its own and increasingly becomes a threat to the crew. Those familiar with the film may have deep-seated reservations about AI …
The Smart Process Manufacturing Congress 2020 was held under the motto “Demystifying digitalization” and thus moved between extremes: The optimistic, euphoric promises of the propagandists of digital transformation and the reservations of some practitioners about black-box models that are not always comprehensible. Above all, the focus was on the question: What is the best way to unite the digital world with the real world?
In the Corona year, the congress was held for the first time in a purely digital format. To pick up on a technology point right away: The sometimes-bumpy implementation revealed more than any white paper or lecture on the topic of “digitization,” how important the repeatedly voiced demands for interface standards and data connectivity really are.
In terms of content, it was surprising how much weight is now being given to the insight that the success of digital transformation is primarily a matter of the mindset of the employees involved. Right at the start, a particularly persistent myth was dispelled — that digitization can only be implemented by large corporations for reasons of cost and personnel capacity. Several speakers showed that small and medium-sized companies can also achieve this.
Change — but How?
In his opening keynote speech, Ilja Grzeskowitz addressed the fundamental crux of change (“Everyone wants change, but no one wants to change!”). The quintessence: The change competence of each individual is decisive. Change must be seen as a pleasure, not a frustration. His advice: you have to focus on the things you can actually personally influence and change. “The perfect moment will never come — no one should wait for that; it’s about just starting!” The hype around digital transformation also calls up one or two free riders. Not everything that is now labeled with the cipher “4.0” is actually new. This applies in particular to the electronic collection of data for the optimization of technical equipment.
In the process industry in particular, the degree of automation has been high for years: Without computer-aided production, a chemical production site would already be inconceivable today. The “digital plant” plays a central role in the entire life cycle of an operation. However, it is also clear that the manufacturing industry with its discrete production units is significantly further ahead in terms of digital transformation. What is driving digitization in the process industry are requirements — for example, smaller batches and more individualized products with simultaneously shorter product life cycles.
One way of meeting these requirements is seen in the modularization of process plants (MTP: Module Type Package), confirms Rebecca Vangenechten (Siemens), for example. With the modularization of production, it is possible to concentrate on the recipe and not on the plant and machine technology required for it.
This is a particular advantage in times of frequent and rapid product changes due to new market expectations. Dr. Attila Michael Bilgic (Krohne) agrees — the problem with implementing such new concepts is, of course, that plants in the process industry are usually in operation for much longer than, for example, a production line for smartphones or vehicles.
The Digital Twin
Vangenechten presented how the digital twin can drive the “digital enterprise” - for example, by replacing physical experiments and accelerating the market launch of new products. One thing to keep in mind, he said, is that the virtual twin is not just a product twin; it can also act as a plant twin and a process twin. The advantage of each “twin” is a reduction in the number of physical and analog simulations and tests, as well as the associated costs.
Frank Schöggl and Michael Strack (both from Yncoris) are also working intensively on the digital twin: the production twin of a cooling tower was presented. The customer benefit is the prediction of the cooling water flow temperature. Ultimately, the result is an optimized periodic operating strategy and a minimization of the energy requirement, taking into account the permissible fluctuation range and assured average temperature.
Dr. Wilhelm Otten (Evonik), as a member of the Namur Board, spoke about the importance of harmonization and standardization. This avoids unnecessary complexity, and new technologies can be used more efficiently to achieve end-to-end automation of value chains.
Where do Plant Manufacturers Stand?
Prof. Dr.-Ing. Gerrit Sames (Technical University of Central Hesse) addressed a study on the topic of “Digitalization in medium-sized companies” and drew a sobering balance: medium-sized companies are stuck in tradition — opportunities through digitalization of business models are still largely untapped. The strong product focus of the machine and plant manufacturers, which is the reason for the successes of the past, threatens to become a disadvantage. While product features are losing importance, new service business models are becoming more important — a 40-40 split is expected in the future.
Sames observes that customers attach less importance to specific product features because these rarely meet their needs — this is where digitization should enable more flexibility. However, this has so far been the exception rather than the rule in SMEs: even digital support during the ordering process is by no means the norm. Offers relating to condition monitoring or predictive monitoring are also rare. No wonder that 75 per cent of companies do not offer digital training or webinars. Concepts such as “pay per use” play virtually no role. In short, the level of digitization determined for SMEs gives little reason for euphoria. (Note: The survey shows the status as of 2018; significant variables are unlikely to have changed).
But how can the flood of data be compressed so that it is tradable and becomes knowledge? Bilgic tackled this question of all questions: He presented very practical answers — for example, one should refrain from repeatedly converting data into new formats, as there is always the danger that important information will be lost. In particular, the constant switching between digital signals and their conversion into analog signals can be harmful. This can be prevented by using Ethernet APL (a communication technology developed specifically for the requirements of the process industry), says the expert.
Another important step, he said, is to communicate to the expert in question only data that is relevant to his task (contextual approach). Last but not least, we should accept that the performance of a computer today is higher than that of a human being. Another point: focus and act as locally as possible. The philosophy of centralized control should be abandoned and the aspect of local intelligence strengthened.
Acceptance and Qualification
Not everyone can understand everything — that’s why communication must improve and technology must become simpler. Robert Tordy (Virtual Fort Knox) and Uwe Beyer (Beyer & Kaulich Unternehmensberatung) emphasized that even after the installation of digital technologies, operations depend to a large extent on employee acceptance and qualification. A “translator” is very important here, for example between the practical language of the company and the technical language of the management.
Ingo Hild (Osram) showed with his contribution “Lean and Digital” which building blocks and approaches help companies to advance in terms of digitalization. The Osram pilot plant in Schwabmünchen, Germany produces preliminary products such as phosphors, filaments and metallic housings. Hild describes the ever-shorter product lifetimes as a challenge - while the incandescent lamp has been continuously developed over decades, new system solutions are now required at ever shorter intervals.
For Hild, lean management is the basis for this: “First design the processes efficiently, then set up digitization!” The philosophy: Smart Factory is 70 per cent employee mindset. The plant and operations manager describes how the amount of available data virtually exploded during digitization. That’s why the topic of analytics became very important: “New iterative cycles are always necessary, which are analyzed by an interdisciplinary team.” Again, the speaker suggested that starting with smaller projects is promising. Hild also noted that the “D” in the term digitization stands for “Do it.”
Data-based decisions are the foundation for successful digitization initiatives: Frank Hertling (Bilfinger Digital Next) described how companies achieve “Digital Operational Excellence” — despite all the constraints in a Vuca world [Vuca: V=Volatile (Volatility) / U=Uncertainty (Uncertainty) / C=Complexity (Complexity) / A=Ambiguity (Ambiguity)]. How to live with all these rapid changes? It only works through more Clarity! In other words, sharpening the focus, communicating processes and interrelationships clearly.
Data Clarity Required
Until now, employees have made a good living from their domain expertise; now data expertise must be added. In addition, a scalable IT infrastructure is becoming increasingly important in order to be able to react more quickly to changes of any kind. Last but not least, knowledge management is of great importance: “Knowledge must be shared!
It often remains difficult to bring together the right data from different sources and turn it into valuable information with the necessary expertise and monitoring and analysis tools. Hertling used specific examples to describe how he and his team found impressive solutions. For example, one task was: How can we shorten the production time of a mixing process without introducing a new shift? Thanks to data analysis, a 10 per cent increase in productivity was achieved. At another company, which was operating almost permanently in overload, an analysis of the causes of breakdowns made it possible to announce 90 per cent of the expected breakdowns to the personnel ten minutes in advance.
Dulaan Punsag-Odefey (Samson) dealt with the benefits of extended monitoring - the solution presented, Sam Guard, does not monitor a pump or an individual heat exchanger, but keeps an eye on the entire plant, according to the speaker. “Analytical monitoring” is what experts call the ability to monitor all processes and devices in a plant at once. The characteristic feature of this is not to pay attention to limit values, but to detect changes in the direction of limit values. For example, two different vibration values at different measuring points can be interesting in this context, with neither measuring point reaching the limit value — but the correlation between the two values can indicate a deviation.
Dr. Claus Neubauer and Ralph Grothmann (both from Siemens) described the state of the art in terms of “artificial intelligence in the industry.” According to them, it is not only important to detect faults or predict failures; there must always be a recommended course of action associated with it — even if this involves a certain degree of uncertainty. As a more recent development, they described the so-called contextualization, i.e., bringing together process data with other data from the process environment. An interesting approach is the integration of visual optical quality data into digital transformation (interesting, for example, for the qualification of food, fruit, etc.). The starting point of such analyses is, of course, always visual material generated via appropriate cameras.
Digitization? Just do it!
Conclusion: Compared to the previous year, the purely digital Congress 2020 offered a wealth of suggestions and best practice examples. Basically, all speakers also encouraged small and medium-sized companies to embark on the digital transformation — “just do it,” is the advice. A key message on this: The most important success factor for digital transformation is often not the tool or the software used, it is the people and their mindset.
Speaking of people, the discussions after the presentations and during the breaks were sorely missed at this year’s digital congress — what is often just said (or written) is true in these times. The personal encounter remains important and is in part irreplaceable.
* * The author is freelancer for PROCESS
(ID:47124540)