:quality(80)/images.vogel.de/vogelonline/bdb/1794200/1794278/original.jpg)
CO2 Use for Polymers CO2 Use on the Verge of a Breakthrough? Study Examines the Potential
For years, the industry has been working on recycling CO2 as a raw material. Is there a breakthrough now? In its new technology and trend report ‘Carbon Dioxide (CO2) as Chemical Feedstock for Polymers - Technologies, Polymers, Developers and Producers’, the Nova Institute talks about an installed production capacity of 850 kt/a. The authors examine which technologies are available and who the main players are.
Related Companies
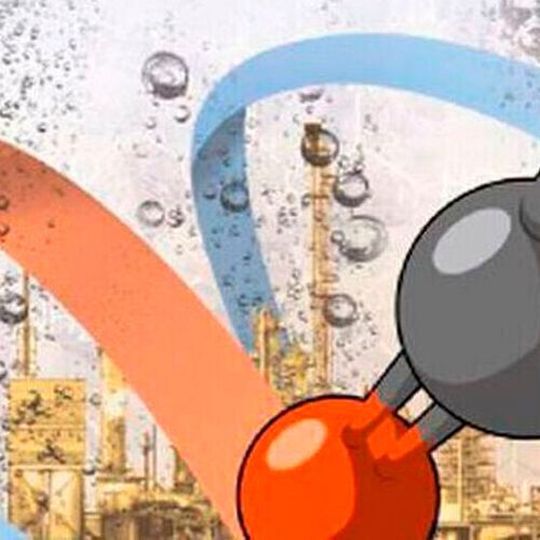
Plastics have ruled the world for decades: without the versatile polymers there would be no packaging, no car fittings, no PC housing and no smartphone. 400 million tons of polymers are produced worldwide every year. The quantity has been growing by three to four per cent per year for decades - and the trend is upwards. Nevertheless, plastics have fallen into disrepute: they consist of 90 per cent fossil raw materials and at the end of their life cycle they release the climate pollutant CO2.
The crux of the matter: decarbonization does not work here, after all, the backbone of a polymer chain is carbon and thus not only the main component but also the functional carrier. So, what could be more obvious than to use the climate killer itself as a raw material for plastics production?
CO2 as a Raw Material - What is State of the Art?
Researchers and companies have been working on this for years, but success stories about the successful use of CO2 as a material are few and far between. In Germany, Covestro is the ‘frontrunner’ here. Since 2016, a production plant has been in operation in Dormagen that is expected to produce 5,000 tons of polyol per year.
A European project consortium under the acronym BECCU is pursuing a particularly ambitious goal: here the focus is on proof-of-concept for integrated production with CO2 from biomass and water electrolysis: in which electricity, heat, fuels and plastics such as polyols are at the centre.
In Niederaussem, the consortium of the European project ‘Align-CCUS’ has commissioned a CCU demonstration plant. Here, CO2 from the flue gas of the neighbouring 1,000 MW lignite-fired unit of the Niederaussem power plant is converted into the fuel DME.
BASF is also working on a process for producing the absorber raw material sodium acrylate from ethene and CO2 and is operating a mini-plant.
According to research by the Nova Institute, most of the plant capacity is in China.
Here, they have kept a close eye on the worldwide projects around CO2 and have closely examined the state of the art in their new technology and trend report ‘Carbon Dioxide (CO2) as Chemical Feedstock for Polymers - Technologies, Polymers, Developers and Producers’: Which polymers can be produced from CO2, and with which processes? How far have the technologies already been developed, matured and implemented in pilot, demonstration and (semi-)commercial plants? Which companies and institutes are working on technologies to produce polymers or building blocks from CO2?
Even if there are already successfully implemented technologies in the market or on the verge of commercialization, the authors name many technical hurdles that still have to be overcome in order to use new CO2 conversion plants on a large scale.
Production capacities for CO2-based polymers have increased in recent years, the authors researched. According to the study, production capacities, mainly for polycarbonate and polyol for polyurethane production, are now around 850 kilotons per year, with an average weighted CO2-based carbon content of only 5.4 per cent so far. The calculations are based on the capacities of nine companies whose sites are mainly located in Asia, Europe and North America.
The third version of the Nova Institute's Technology and Trends Report aims to provide a comprehensive overview in 100 pages of the various production routes of CO2-based polymers that are being developed and commercialized by research groups of main players in the industry, start-ups and institutes.
(ID:47118001)