:quality(80)/images.vogel.de/vogelonline/bdb/1784500/1784507/original.jpg)
Market Trend Digital Twin Solutions is Now the New Normal
Covid-19 has transformed industries like never before and the oil and gas sector is no exception to this. The demand for digital twin technologies is at an all-time high amidst the pandemic and major industry players are already making use of this technology for numerous significant projects.
Related Company
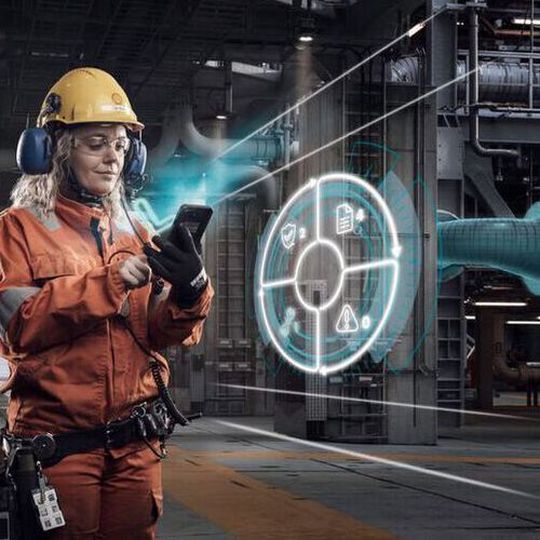
The global digital twin market size was valued at 3.1 billion dollars in 2020 and is projected to reach 48.2 billion by 2026. It is expected to grow at a CAGR of 58 % during the forecast period, states a report by the research tech-driven company Report Linker. This year was dominated by the Covid-19 pandemic which led social distancing to become the new normal; in this scenario the demand for digital twin technologies in the oil and gas industry increased.
Agreeing to this, Anne-Marie Walters, Global Marketing Director, Bentley Systems, said, “Before the pandemic, we were seeing an increasing interest in the use of digital twins in the oil and gas industry. Now, this year, there has been an explosion in growth and interest.” The adoption of Internet of Things (IOT) and big data analytics across the industry has further contributed to the rise of the digital twin technology.
Leading oil and gas corporations have already integrated digital twin solutions in their assets. For instance, Royal Dutch Shell, one of the biggest players in the industry is employing the technology in order to make its existing assets more competitive and operations more reliable and safe. “Deployment of digital twin will be targeted at all assets in Shell starting with upstream, integrated gas and downstream,” shares Stefan Irrgang, Global Process Owner Integrity & Reliability Decision Executive Digital Twin, Shell.
Shell’s Nyhamna Gas Plant
In Norway, Shell’s Nyhamna gas plant brings data and people closer together as it provides continuous information on optimal process conditions. The plant is a highly dynamic gas processing facility where gas arrival conditions and equipment status are in constant change. Irrgang explains, “The digital twin technology allows us to explore the operating envelope of Nyhamna both under stable operation and in transitions between one operations scenario to the next. This opens up a completely new way of performing optimisation, where the ultimate objective is to maximise gas and condensate production as well as minimise energy consumption, while reducing maintenance need and avoiding breakdown of equipment.”
He adds, “By running ‘what if’ simulations, the Operations Support team together with the Control Room can take faster and more accurate process change decisions. This will enable us to choose optimum plant configuration, directly quantify the effects and thus increase the plant’s performance.”
Some of the other assets and projects for which the firm is currently using the digital twin technology are the Pulau Bukom Refinery, Singapore (Downstream Manufacturing); Scotford Complex, Canada (Downstream Manufacturing); Pearl GTL, Qatar (Integrated Gas); Shell Trinidad & Tobago (Integrated Gas); Shell Polymers Monaca, USA (Capital Projects); Canada LNG (Capital Projects) and Ormen Lange, Norway (Capital Projects). Shell has an enterprise agreement with Kongsberg Digital for digital twin integration & visualisation software across its assets and capital projects.
Indonesia’s Maiden Petrochemical Digital Twin
In Indonesia, the first petrochemical digital twin is being built for Chandra Asri – the country’s largest privately held petrochemical company and sole domestic producer of Styrene Monomer and Butadiene. Bentley Systems and Siemens have been appointed for the task.
“Adhering to industry leading open standards, Chandra Asri receives integration with enterprise information systems (including SAP EAM), operational technologies (IOT and their data historian, Osisoft Pi), and engineering and document management systems including Open Text, all managed within a changing environment,” shares Sandra Di Matteo, Director of Marketing – Digital Twin Solutions (Industrial), Bentley Systems. “Structured metadata (or an asset information model or tag registry) is maintained in a central system with controlled access and relationships maintained between systems. The central system allows access to accurate, intelligent, and smart 3D models, engineering data, and historical information (operations and maintenance).”
Chandra Asri establishes the foundation of engineering information management and ensures the integrity of the underlying data before adding the visualisation aspect to the digital twin. This process enables informed-decision support from capital planning through proactive asset maintenance, mitigating risks to improve plant safety and increasing operational efficiency, as well as ensuring regulatory compliance.
Mega ‘Predictive Maintenance’ Project in Progress
Abu Dhabi National Oil Company’s (Adnoc) ‘Predictive Maintenance’ project is scheduled to be one of the largest in the oil and gas industry and aims to optimise asset efficiency across its upstream and downstream operations. Supported by the digital twin technology and machine learning, the project will help to predict equipment stoppages, reduce unplanned equipment maintenance and downtime, increase reliability and safety, and is expected to deliver maintenance savings by up to 20 %. The Gulf-based nation is already witnessing several operational benefits and cost savings from the project.
The first of the four-phase project has been completed and includes the modeling and monitoring of 160 major turbines, motors, centrifugal pumps and compressors of six Adnoc Group companies. On completion, the project will assist the central monitoring of up to 2,500 critical machines across all Group companies. Expected to be completed by 2022, the predictive maintenance project is being built in partnership with Honeywell.
Challenges
The application of digital twin in the industry comes with its own set of challenges. Firstly, the management has to be convinced. “It is important to clearly showcase the benefits to assets, teams and individuals. In Shell, assets led the local deployment while the global team defined the enterprise technology and standards,” mentions Irrgang. He adds that it is vital that assets understood that digital twin is not just another IT application. It is an end to end integrated solution which has the potential to transform the ways of working from today into the future.
Another key obstacle is an overwhelming amount of existing data. Walters states, “Sorting through this information and working out what is valuable for making good decisions, along with agreeing how best to standardise asset information across many different departments is challenging. Until recently, scaling fast has been a major hurdle. Every company that I know can point to many successful digitalisation pilot projects, but few have been scalable across the enterprise.”
With the oil & gas industry incorporating digital twin technology across diverse segments, it has certainly become the new normal in the sector and with time is only expected to attract more followers.
* The author is an editor at PROCESS Worldwide. Contact: ahlam.rais@vogel.com
(ID:47063004)