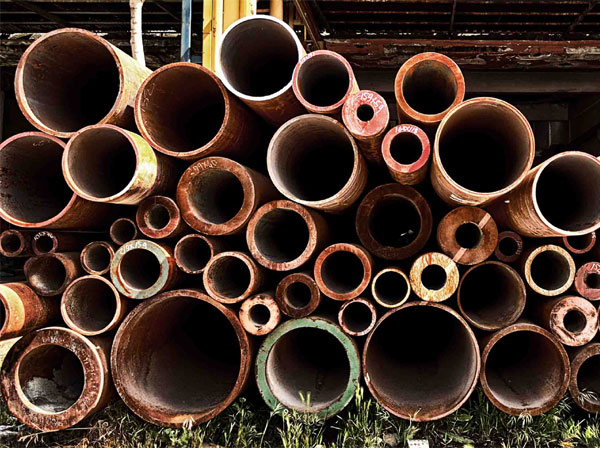
India is the seventh-largest country in the world, with a total area of 3,287,263 square km. It has a land frontier of 15,200 km and importantly a coastline of 7,516.6 km. This is just an indication of how much India is exposed to global warming which is set to severely impact buildings, dams, roads, bridges, automobile railway, energy and petroleum sectors.
Global climate change is one of the most important concern for world governments and is a major research subject for the international scientific community with the participation of multi and interdisciplinary groups. Two fundamental reports — The United Nations Intergovernmental Panel on Climate Change (IPCC) and the N. Stern, The Economics of Climate Change, 2007 Cambridge University Press, UK — outline parameters that will affect infrastructure, temperature change, atmospheric moisture change, sea level raise, wind, desertification, pollution and inclusive biological infestation. With the rise in temperatures, the melting of polar and glacial ice and snow and also increase in the thermal expansion of seawater is taking place. This is resulting in an irregular global increase of moisture, resulting in higher humidity. All the infrastructure that is close to coastal lines is set to be impacted and it’s already visible.
Temperatures change is gradually resulting in extreme climate, changing the periodicity of climate cycles. Such extreme climate events are bringing detrimental effect by way of corrosion and also bio-deterioration. This is also damaging both metallic and non-metallic materials used in infrastructure construction.
Many studies have elaborated the impact on structures due to global warming and their exposure to corrosion. Reinforced concrete (RC) structures are subjected to environment actions affecting their performance, serviceability and safety. Among these actions, chloride ingress and carbonation lead to corrosion of reinforcing bars that reduce the service life of RC structures. Evidence indicate that carbonation and chloride ingress are highly influenced by environmental and climatic conditions of the surrounding environment — atmospheric Co2 concentration, temperature and humidity.
According to the International Panel of Climate Change (IPCC), the uncertainty of climate projection is high. The studies have estimated that environmental CO2 concentration could increase enormously in the next 10 years. The changes in environmental temperature, relative humidity and carbon dioxide concentration can increase corrosion risks resulting in more widespread corrosion damages and loss of structural safety. This is set to impact the safety of billions of people globally, India too is not excluded.
Impact on China
China is facing its own impact. An investigation of carbonation-induced deterioration in three typical Chinese cities — Kunming, Xiamen and Jinan — is an example. By 2100, mean carbonation may increase by up to 45 per cent for RC structures in China due to change in climate. This is pushing China to develop and implement climate adaptable strategies through the improved design of concrete structures and making them corrosion resistant.
Many sectors are set to be impacted due to global warming, which is actually a global warning.
On petroleum sector
The petroleum industry has been back-bone of the world economy for the last more than 60 years. The United States has been the world leader in petroleum engineering technology. But globally, the biggest challenge in assuring petroleum flow through pipelines has been corrosion problems.
In India, the cost of corrosion and scaling presents anything from 30 per cent (mainland) to 60 per cent (offshore) of the total maintenance expenditure. This squeezes the petroleum industry that is responsible for driving energy sector.
A large tranche of petroleum infrastructure and maintenance costs relates to production operation, mainly in assuring flow from the wellbore to the processing plants, refineries, and oil tankers. Millions of dollars are spent annually to ensure that access to processing plants, refineries, storage sites, and oil tankers is free of leaks or plugging.
In a federal study, a total cost of $275 billion was attributed to corrosion way back in the year 2002. This presented a rise of $100 billion in the next five years, approximately 3.1 per cent of the GDP, which is subtotal of its entire agricultural and mining components.
US Congress was sufficiently alarmed so as to enact a “Corrosion Prevention Act” (2007), offering a tax incentive of 50 per cent to companies who invest in corrosion abatement and prevention. Post petroleum sector in US, Department of Defense carries the biggest budget of corrosion cost.
Coastal infra at risk
Coastal salts can create a corrosive environment for any infrastructure across the world, the reason being humid and saline climate.
When steel reinforcement corrodes, the corroded product occupies more than three times the volume of the original steel, exerting great disruptive tensile stress on the surrounding concrete, leading to further cracking, more weather access and further corrosion.
According to the American Institute of Architects, it is essential to use hot dip galvanised steel, to make such coastal infrastructure decay resistant.
On Indian Railways
The fourth largest rail network in the world, Indian Railways, comprises 125,000 km of track length over a route of 67,312 km. More than 50 per cent of the route are electrified. Indian Railways has about 1.35 Lakh bridges and about 800 are most important. Almost all the infrastructure of Indian Railways is exposed to humidity, dust and extreme change in climate. It is already struggling due to huge expanses in replacement and repairing. The annual loss due to pre-replacement of corroded rails is huge about Rs 440 crore. Many accidents have been attributed to corrosion of “fish-plates”. Experts have estimated losses of almost 4 per cent of GDP per year on account of corrosion which may be avoided if the railway tracks are galvanised.
Corrosion reduces the life of rail to nearly half its expected life.
On automobiles
Globally the top brands in cars started galvanising various parts of the cars, including the body to fight corrosion issues. This brought safety to the cars and protection to the environment and strengthened the economy.
By 1987, what became standard was a 10-year perforation and five-year cosmetic warranty from all the North American, European and Japanese automakers for vehicles sold in the North American market.
Indian car manufacturers use about 3 per cent galvanised steel for domestic market. However, the same Indian car manufacturers use over 70 per cent galvanised steel for the same models they export to markets in Europe, Asia and Africa, produced from the same stamping and assembly facilities. Indian consumers are not getting it, because they are not demanding for.
Car makers in Europe, North America, Korea and Japan have been using galvanised steel for body panels for decades and provide anti-corrosion and perforation warranties for a minimum of 10 years. More than 60 per cent of the cars in India have surface rust which reduces steel strength and the life of the car.
On energy sector
We are moving towards 100 per cent electricity in villages across India. “Light in every house” is India’s vision. But how much sustainable it is going to be would need to be assessed.
According to the American Iron and Steel Institute, close to 1 million steel distribution poles have been installed in the United States since 1998 and are being used by more than 600 US electric utilities. India might be having more poles but how many are corrosion resistant is still to be assessed. This is one sector that is extremely exposed to vivid climate conditions.
(The writer is CEO, Hindustan Zinc)