Kozhikode: Wooden dhows, known as Uru in Malabar, arguably the biggest handicraft in the world, continue to enthrall millionaires of Arab nations. A sleepy town on the west coast of Kozhikode, Beypore is the prime centre of this marvelous craftsmanship.
After rolling out a record breaking wooden dhow which measured 200-feet in length, Binafa Enterprises, one of only two wooden dhow manufacturers in Beypore, is now preparing to deliver another marvelous 148-foot-long wooden dhow to a Qatari millionaire.
The wooden dhow, named Al Rahi, would be launched to the river on 15 January, in a traditional ceremony, where the Mopla Khalasis of Beypore would use a manual winch to pull the 300-tonne weighing craft to the Chaliyar River.
The Qatari industrialist named Khalid ordered this passenger boat at an estimated cost of over Rs 10 crore in 2015. Since then, thirty skilled carpenters have been working on this project. Binafa Enterprises managing director Pandikasalakandiyil Abdul Gafoor is reluctant to reveal more about his customer.
He feels this expensive purchase could draw severe criticism in Qatar which is going through a tough time, financially. “Many still see owning a wooden dhow as a luxury. We have one more confirmed order from the same family for another Uru. So I am not in a position to reveal the details of the customer," said Gafoor, sitting in his office at Palayam, Kozhikode.
Al Rahi will have the distinction of being the first completely furnished wooden dhow to have been made in India. Earlier, the interiors were completed at the destination. Al Rahi will leave the Beypore coast with luxurious interiors. The voyage from Beypore to Qatar, which is expected to take several weeks, would cost around Rs 25 lakh, which the businessman will have to pay for as well.
Al Rahi will be launched in to the Chaliyar River from its manufacturing yard at Karuvanthiruthi, near Beypore on 15 January. The boat will remain on the banks of Chaliyar for two more months to allow the interior work to be completed.
“It is expensive, but when compared to steel or fibre boats, wooden dhows can be used for two or three generations if the boat is maintained well. The maintenance cost is slightly higher for wooden dhows,” Gafoor said. The average lifespan of a steel boat is around 25 years and that of a fibre yacht is 40 years.
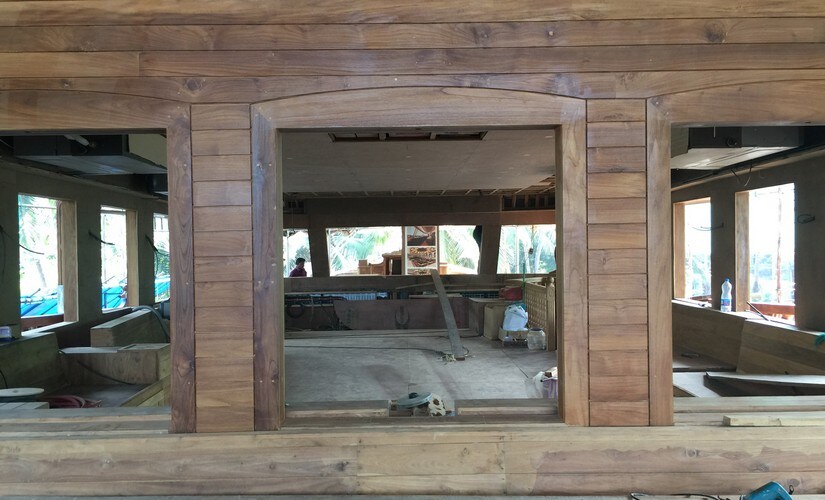
First floor of the three-storied dhow is the sitting area for passengers . Image courtesy: K Praveen Kumar
The yacht, made in the Sampok style, which is a Qatari yacht design, but with open rear platforms, was completely made of teak wood, which the manufacturers personally selected from private properties in and around Kozhikode.
“We can use only the best teak wood and we selected the best trees from private properties. We used in excess of 15,000 cubic feet of wood for the boat,” Puzhakkara Rameshan, the chief carpenter or maistry as he is called, said. Rameshan is the carpenter-cum-engineer of the wooden dhow. He takes care of design, mounting engines and installing navigational and safety equipment.
“Rameshan and his uncle Puzhakkara Sreedharan are the only remaining chiefs in Uru making. Without them, we cannot make this supreme handicraft. The younger ones of these families are carpenters,” said Gafoor. He adds that Uru making is a team effort and he is a facilitator. Rameshan has already fixed two 850 BHP Yanmar engines which were imported from Japan. Now, his workers are giving final touches to the plumbing and electrical work.
Beypore, the Arab connection and Wooden Dhow making
The art of Uru making in Beypore goes back to the beginning of the maritime history of India and the spice trade with Mesopotamia.
Arabs were masters in construction of wooden dhows and the early Arab traders who visited the coast of Malabar for export of spices, taught the techniques of Uru making to select Beypore carpenters. The master craftsmen of Beypore soon outshone their Arab counterparts and started building the best wooden dhows with magnificent wooden keels that could withstand roughest of seas.
“Until recently, all wooden dhows we built were cargo boats. Arabs taught us the craft so that they could build Urus here and transport spice loads from our coast. My father Pandikasalakandiyil Achamu Haji was the one who brought us in to the field of Uru manufacturing,” Pandikasalakandiyil Abdul Majeed, father of Abdul Gafoor said. Now, most orders to Beypore are for passenger boats, Majeed added.
Availability of superior quality teak wood from Nilambur forests could have been one reason why Arabs selected Beypore for construction of wooden dhows. The deep waters of Chaliyar River and availability of a port also attracted Arabs to Beypore. Andikutty maistry from Beypore was one of the first carpentry chiefs who learnt the art of wooden dhow making from the Arabs. Chandukutty maistry also mastered the art. Puzhakkara Rameshan and Sreedharan are the only remaining maistrys who know the art.
When the traditional maritime trade with Arabs turned to modern transport methods, wooden dhow making was also badly hit. “Manufacturing of Urus came to a halt post 1970. Not a single Uru was built for the next 10-15 years. During 80s, Arabs started manufacturing wooden dhows in Arab countries but the lack of technique to launch it in to the river forced them to seek help from our people. Beypore slowly regained the prominence in Uru making", Gafoor said.
Though many tour liners and millionaires in other parts of the world are keen to acquire these pieces of art, a lack maintenance facilities stops them from buying them. Arabs are usually the prime customers. One notable exception: An Uru was recently delivered to France for PA Ibrahim Haji.
Dockyard workers keep the trade in Beypore
Apart from Arab countries and Beypore, Indonesia, Mangalore and Gujarat now manufacture wooden dhows. However, with no Mopla Khalasis (dockyard workers) available there, they don't know how to launch the dhow into the river. “That's the most crucial part. We can't use any mechanical equipment as the dhow has a flexible structure. An unwanted jerk could cause trouble. The manual winch and iron rope mechanism used by Mopla Khalasis is the best and time-tested method,” Gafoor said.
In Mangalore, dhow makers place metal sheets below the dhow till the river and then pour grease on the plates. An earth mover is then used to push the dhow, which skids through the grease, swaying from side to side, until it enters the river. Using this method, the dhow suffers change in shape and workers use ropes from both sides to pull and balance the shape of the dhow. In Indonesia, they use hammers to hit the boat into the river, which also causes considerable damage to the dhow.
Mopla Khalasis have stunned the world on many occasion with their technique. Beypore Khalasis hit national headlines when they pulled out the derailed coaches of Bangalore-Tiruvananthapuram Central Island Express from Ashtamudi Lake using their traditional pulley-iron rope-manual winch method during the Peruman train accident.
Khalasis were also called in to bring aircraft that skidded off runways and which even sophisticated machinery failed to pull up. “They use Thovar (the manual winch), Uruls (round wooden logs), Baloos (Long hardwood logs), pulley and iron rope. The specialty of Khalasis is that they convert any available material to weight pulling equipment and manage to pull out any amount weight. No other country or place on earth could boast of a better technique which has beaten modern machinery,” Manoj, a supervisor at the Karuvanthiruthi dhow making yard said.
The Thovar or manual winch is made using the trunk of tamarind tree. It's quite a sight to see these skinny Khalasis — with minimum effort and superior balance — launch a 300-tonne dhow to the river in one smooth motion.
“All the Khalasi chiefs in Beypore are well over 60. No new members are being trained. A while ago, we managed to get one youth to enter training. But no one is coming to be trained in this superior traditional method of weight moving,” Gafoor said.
Gafoor said what worries him is that when the remaining Khalasi chiefs are no more, Beypore will lose its prominence in wooden dhow making. “With no Khalasis, we will have to first dig a deep pit and construct the dhow inside. After completion we will have to break the bund and allow river water to enter the pit to make the boat float. But this can cause serious damage to the dhow,” Gafoor said.
Lack of experts threaten this marvelous handicraft
When Rameshan and Sreedharan stop crafting the wooden dhows, a century-old tradition of Beypore may come to an end. There are none left in Beypore, apart from this duo, who know the complete art and engineering of dhow making. “The most important part of the dhow is its keel and design. The first 20 percent of the crafting is very important. The rest is mere carpentry. However, any mistake in the first 20 percent could make the boat useless,” Rameshan said.
For Gafoor, Rameshan is the axis of his business. “Plumbing and electrical works are done by other parties, but everything is done under the supervision of Rameshan. There is not even one square inch of area which was not being touched by a chisel. All calculations and designs have to be approved by him. When there are no chiefs like Rameshan then there is no wooden dhow making,” Gafoor said.
Published Date: Jan 11, 2018 20:12 PM | Updated Date: Jan 11, 2018 20:12 PM