Besides the rush to close their books of accounts for 2016-17, March saw fast-moving consumer goods (FMCG) companies move with haste on another front.
The rush was to set up manufacturing units in Assam to avail of fiscal benefits before the deadline of March 31 lapsed. At a time when the concept of tax havens is set to vanish following the implementation of the goods and services tax (GST) by July, the rush, say experts, was reminiscent of a similar one earlier to Himachal Pradesh and Uttarakhand, which were offering sops to woo industry.
While the financial incentives — a 10-year tax holiday in the case of Himachal and Uttarakhand — expired in 2010, Assam’s excise benefits by way of tax refunds were on till the end of March. Those who set up plants before March 31 this year would get excise benefits for the next 10 years.
FMCG companies from Hindustan Unilever (HUL) to Patanjali, Dabur to Marico, Jyothy Labs, Emami and Bajaj Corp were in no mood to ignore this opportunity, say experts. They invested nearly Rs 3,000 crore of total investments in Assam in the past few months to set up plants, say industry experts. February-March saw most of these units begin commercial production.
HUL, for instance, set up its new facility at an investment of Rs 1,000 crore, near its existing factory at Dooma. “It will augment the production capacity of personal care products for the company,” the firm said in a statement on March 21.
HUL first entered Assam in 2001, setting up three units to make shampoos, skin creams and toothpaste. “With over 15 years of operating experience in the state and considering the support from the state government and the local community, HUL has decided to set up a new manufacturing unit in Assam,” HUL had said earlier.
The country’s largest consumer goods company is not the only one to feel this way. Dabur India Chief Executive Officer Sunil Duggal also believes the state is ideal to cater to not only the eastern belt, but also parts of the north. The company last week inaugurated a new plant at Tezpur, at a cost of nearly Rs 300 crore to produce health care, personal care and home care products. “The Assam market itself is underpenetrated. So accessing that market at an economical cost is now possible. Plus, not only can it act as a hub for the eastern belt, but parts of the north such as Uttar Pradesh can also be catered to from there,” he said.
Tax havens, say experts, also act as zones where firms can set up incremental capacity and Jammu & Kashmir, where excise benefits will continue till 2020, is also expected to be exploited for the same purpose. Dabur, for instance, has land in Jammu, but is yet to take a call on setting up a unit there.
While manufacturing on an annual basis is outsourced to third-party players by FMCG companies, this is to the extent of about 15-20 per cent, say sector experts. The rest is undertaken in-house, to ensure production and quality standards are intact, they say.
Sumit Malhotra, managing director, Bajaj Corp, the maker of products such as Bajaj Almond Drops Hair Oil, which began commercial production at its new unit in Guwahati on March 15, said the plant can cater to 21 per cent of its hair oil demand.
“While we have plants elsewhere in the country, the advantage of setting up a manufacturing base in places such as Assam is that the fiscal benefits will stand post introduction of GST for a period of 10 years. That is a huge relief for companies,” he said.
The revenue foregone by the Centre by way of area-based excise duty exemptions was Rs 19,120 crore in financial year 2015-16. This was marginally lower than the previous year (FY15), when it was Rs 19,978 crore. Figures for 2016-17 were not immediately available.
Emami Ltd’s executive director, Harsh Agarwal, said past experience also helps when setting up a new unit in a state. “We’ve been in Assam for over 15-20 years now (with two plants) and have strong roots there. Setting up a third unit therefore in the state was not a challenge, since we have good understanding of the market there.” Emami’s third unit was commissioned in February this year at a cost of Rs 300 crore. It is Emami’s largest plant and the eighth by number nationally.
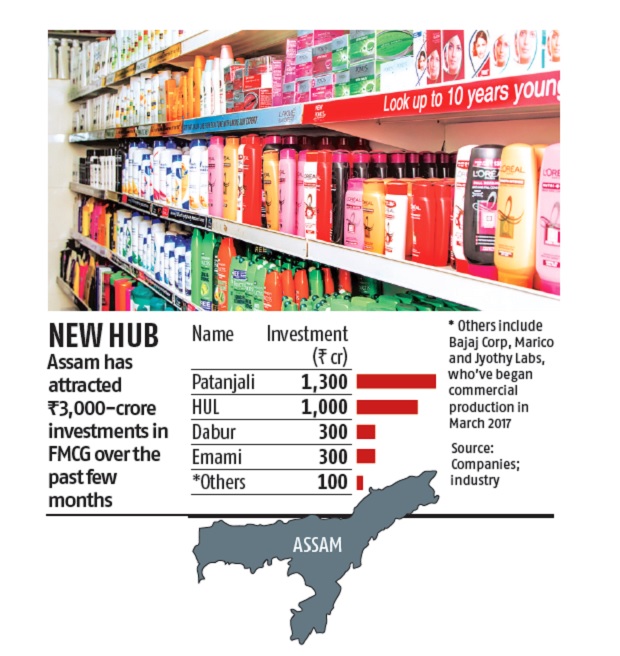